Si : un des principaux constituants de la géosphère et de la technosphère
Le silicium, de symbole Si, ne fait pas partie de la famille des métaux. Cependant, son aspect métallique et son utilisation importante dans les alliages d'aluminium font qu’on le nomme « silicium métal » lorsqu’il est en fragments de pureté supérieure à 96 %. Peu conducteur de l’électricité, on le classe dans la famille des métalloïdes aux côtés du bore, du germanium, de l’arsenic, de l’antimoine, et du tellure. Le silicium se distingue d’abord des autres métalloïdes par son abondance géologique. En effet, il est le 3ème élément le plus abondant dans le globe terrestre et le 2ème élément le plus abondant dans la croûte terrestre1. On ne l’y trouve cependant presque jamais à l’état de corps pur simple à cause de sa grande réactivité avec l’oxygène. En combinaison avec ce dernier, le silicium forme l’ion tétraédrique [SiO4]4-, brique élémentaire des minéraux de la très grande famille des silicates. Les silicates, minéraux à base d'oxydes de silicium associés à des oxydes métalliques, constituent près de 97 % de la croûte terrestre. A ce titre, l'élément Si est un des plus extraits par l’Homme, principalement sous la forme de quartz. En 2017, le groupe d'experts internationaux sur les ressources estime qu’environ 35 à 40 Gt (gigatonnes ou milliards de tonnes) de matériaux silicatés ont été extraites du sol terrestre [1], soit un contenu d’environ 15 à 20 Gt de silicium. C’est trois fois plus que l’extraction de l’ensemble des combustibles fossiles (pétrole, gaz, charbon) observée la même année. Ces matériaux ont principalement été utilisés dans le bâtiment mais une grande partie est restée à l'état de stériles d'extraction. Chaque année, seule une fraction de ces matériaux (< 1/1000) est transformée en silicium métal.
L’élément silicium est également un des principaux constituants de la technosphère. Combiné à d’autres éléments comme le l’oxygène, le fer, le calcium, le manganèse, le carbone, ou l’hydrogène, l'élément silicium est capable de former des matériaux de natures très variées allant du verre (silice SiO2), aux alliages métalliques (ferrosilicium Fe-Si, silico-calcium Ca-Si, silicomanganèse Si-Mn), en passant par les silicones (Si–O), les céramiques (carbure de silicium SiC, nitrure de silicium Si3N4), et les gaz (silanes SinH2n+2). Cet article porte spécifiquement sur la forme simple du silicium : le silicium « métal ».
Des usages différents selon la pureté
En 2019, la consommation mondiale de silicium métal a été d’environ 3 Mt (millions de tonnes). Ceci représente un marché d’environ 7 GUS$ (milliards de dollars US). Les secteurs principaux d’utilisation du silicium métal sont les alliages d’aluminium, les silicones, le solaire et la microélectronique (répartition donnée à titre indicatif dans le diagramme ci-dessous).
Dans les alliages d’aluminium, le silicium métal améliore la coulabilité et réduit le coefficient de dilatation thermique. Les alliages Al-Si sont utilisés dans l’automobile, l’aviation, le transport maritime, le bâtiment, les équipements ménagers, les câbles électriques, et les emballages. Ils sont généralement fabriqués à partir de silicium métal de qualité métallurgique, dit « MG », d'une pureté proche de 99 %.
Les silicones sont des polymères composés de chaînes Si-O. Ils forment des matériaux techniques aux textures très variées : huile, gel, résine, gomme. Leur fabrication fait intervenir le silicium métal de pureté généralement inférieure à 99,9 % (ou « 3N » pour le nombre total de 9), que l’on transforme en gaz diméthyldichlorosilane.
Dans les cellules photovoltaïques au silicium polycristallin, monocristallin, ou amorphe, les propriétés semi-conductrices du silicium permettent l’effet photoélectrique nécessaire à la production d’électricité. Dans le cas des cellules au Si cristallin, le silicium métal est affiné pour atteindre une pureté de 99,999 9 % (6N) à 99,999 999 9 (9N), correspondant à la qualité solaire, dite « SoG » pour « solar grade ». A l’issu de l’affinage, le silicium métal se trouve dans un état polycristallin de haute pureté. On le nomme alors « polysilicium ». Il subit de nombreux autres traitements dont une recristallisation en lingot, une découpe en plaquettes, et une phase de dopage, avant de pouvoir entrer dans la fabrication d'une cellule photovoltaïque. Dans le cas des cellules au silicium amorphe, le silicium sous forme de gaz silane est déposé directement en phase vapeur par plasma.
Dans la microélectronique, ce sont également les propriétés semi-conductrices du silicium qui permettent le fonctionnement des circuits intégrés ainsi que le stockage et la transmission d’information. Le polysilicium est affiné à un niveau de pureté extrême de 10N à 13N, correspondant à la qualité EG pour « electronic grade »2, avant d’être recristallisé sous forme d’un monocristal cylindrique de très haute précision. Le lingot est par la suite découpé en plaquettes ou « wafers » avant de subir de nombreux traitements physico-chimiques supplémentaires, nécessaires à l'obtention des composants finaux.
Les secteurs d’utilisation du silicium métal bénéficient tous d’une tendance robuste de développement dans les années à venir, ce qui poussait CRU—un cabinet d’intelligence économique—à envisager, avant la pandémie COVID19, une croissance annuelle de la consommation de silicium métal à 4,5 %/an sur les 5 prochaines années. La pandémie ne devrait pas remettre en question la croissance du marché à moyen terme, d'autant que le silicium est pressenti comme un élément très prometteur pour remplacer tout ou partie du graphite dans les anodes des batteries Li-ion, ce qui améliorerait grandement leur densité de charge.
De la silice au silicium métal
Le quartz, matière première de base
Le silicium métal n'est pas extrait en mine. Il est produit à partir de dioxyde de silicium, aussi appelé silice (SiO2). La silice de laquelle est obtenu le silicium métal est extraite en carrière. Elle provient principalement de gisements primaires ou détritiques de quartz. Les roches utilisées doivent répondre à des critères particuliers de composition (SiO2 > 98 %, faibles teneurs en oxyde de fer, plomb, alumine, et TiO2), de granularité (diamètre > 15 mm), et de friabilité, pour pouvoir être utilisées en métallurgie. De ce fait, seuls quelques gisements particuliers approvisionnent la filière silicium métal. Les types de gisements les plus communément exploités sont les galets de quartz, les quartzites, et les filons de quartz. Certains grès très riches en silice sont également exploités, notamment en France [2], [3]. Il n’existe pas d’estimation fiable des ressources et réserves mondiales correspondant à ces gisements, ce qui empêche toute analyse de leur évolution. Cependant, en France, les carriers annoncent des réserves de l’ordre de plusieurs décennies au niveau de la production 2019, pour alimenter la filière silicium métal. Contrairement à une croyance bien établie, le silicium métal n’est jamais produit à partir de sable naturel. En effet, les contraintes techniques liées aux procédés métallurgiques (circulation des gaz, risque de colmatage, impuretés) ne permettent pas son utilisation. En revanche, des sables extra-siliceux de grande pureté sont utilisés pour la fabrication d’équipements (p.ex. creusets), de produits chimiques (p.ex. gel de silice), ou de composants (p.ex. couches de verre) nécessaires à l'affinage du silicium et à la fabrication des produits (plaquettes solaires, microélectroniques, etc.). Ces sables doivent répondre à des critères élevés de pureté, ce qui en restreint les gisements exploitables pour ces applications.
Les matériaux siliceux, souvent volumineux et peu chers, sont historiquement transformés non loin des carrières (qq. centaines de km au plus) afin de limiter les coûts de transport. C'est pourquoi les pays producteurs historiques de silicium métal sont généralement producteurs de quartz de haute pureté. Cependant, le besoin de matériaux de plus en plus qualitatifs, notamment pour les filières solaires et électroniques, poussent certains producteurs de Si métal à importer du quartz de régions plus éloignées. On peut citer la Norvège (Elkem) qui importe du quartz égyptien, l’Islande (PCC) qui importe du quartz polonais, et la France (Ferropem) qui importe du quartz espagnol.
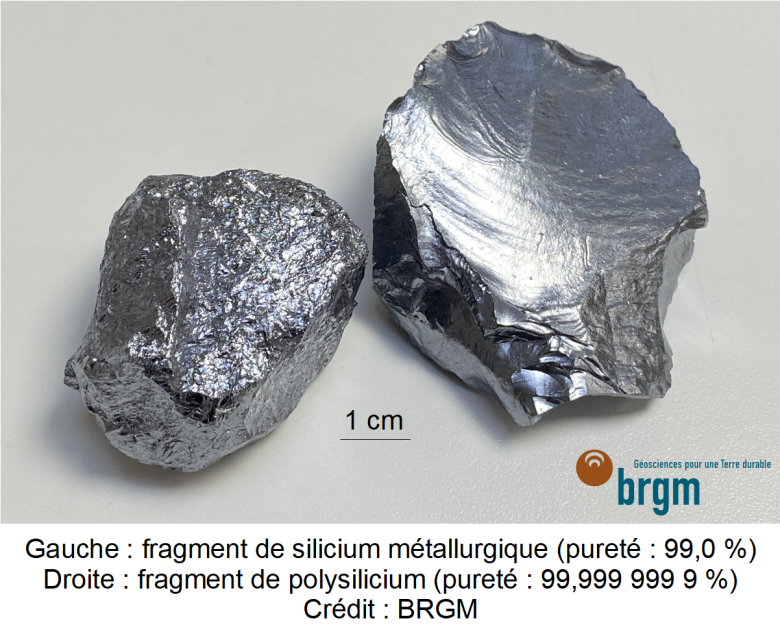
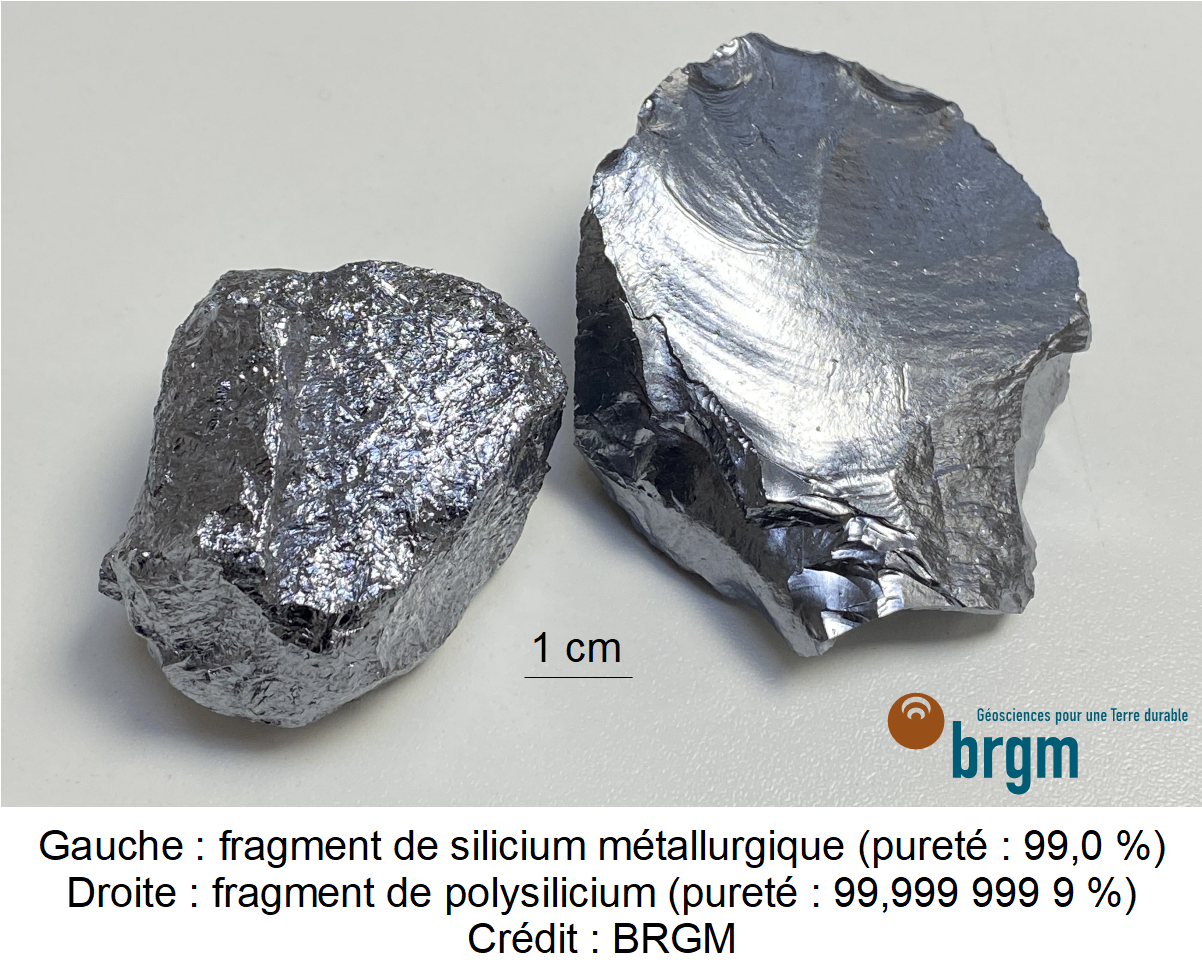
Gauche : fragment de silicium métallurgique (pureté : 99,0 %), Droite : fragment de polysilicium (pureté : 99,999 999 9 %)
© BRGM
Procédé métallurgique
Le silicium métal est obtenu par la carboréduction de la silice, de formule simplifiée :
SiO2 + 2C → Si + 2CO
Des réactions intermédiaires font intervenir le carbure de silicium (SiC), le monoxyde de silicium (SiO), et le monoxyde de carbone (CO), pour donner, dans le fond du four, du silicium sous forme liquide à près de 2000°C. Les réactions se produisent en four à arc électrique et font intervenir en moyenne 2 800 kg de quartz, 1 500 kg de houille (ou mélange avec coke de pétrole), 1 600 kg de copeaux de bois, et 100-150 kg d’électrodes en graphite, pour l’obtention de 1000 kg (1 tonne) de silicium métal de pureté 98,5-99,5 % [4]. Ces 6 tonnes de matières premières solides sont transformées grâce à un apport d’électricité de 11 à 14 MWh, en fonction de la qualité des matières premières3. La réaction produit également de la fumée de silice (env. 400 kg SiO2/t Si métal), du dioxyde de carbone (env. 3 à 5 t CO2/ t Si métal), du méthane, des particules fines, des composés organiques volatils (ex : les hydrocarbures aromatiques polycycliques [HAP]), des traces de métaux lourds et d’autres gaz (SOx, NOx)[5].
Avant d'être coulé en lingots, le silicium métal liquide subit un premier affinage par ajout de laitiers. Ces laitiers oxydent les impuretés principales que sont l'aluminium et le calcium en les solidifiant, ce qui permet de les retirer du silicium liquide. Les lingots solidifiés sont versés sur le sol ce qui donne des fragments de silicium de qualité MG (voir photographie ci-dessous).
L'affinage du polysilicium
Le polysilicium est une forme cristallisée et affinée du silicium métal. Le polysilicium peut être obtenu par différents procédés (Siemens, lit fluidisé, ou hydrométallurgie) offrant chacun ses avantages et ses inconvénients4.
Le procédé majoritaire est le procédé Siemens. Le silicium métal de qualité MG est préalablement transformé en gaz trichlorosilane (ou silane) par réaction avec le chlorure d'hydrogène à 300 °C. Ce gaz est par la suite affiné par distillation fractionnée, puis soufflé sur un filament précurseur en Si extra-pur chauffé à plus de 1 100 °C en présence d'hydrogène. Le trichlorosilane se redécompose alors en chlorure d'hydrogène et en atomes de Si qui se déposent sur le filament à une vitesse inférieure à 1 mm/h selon les données de l'Elémentarium [6]. On obtient finalement des cylindres de silicium polycristallin de pureté 6N à 13N en fonction du secteur de destination. Ils sont par la suite broyés en fragments (voir photographie ci-dessous). A noter que certaines techniques de métallurgie permettent d’obtenir à moindre coût un silicium assez pur pour un usage photovoltaïque sans avoir recours aux procédés chimiques. Il s'agit de la qualité UMG « upgraded metallurgical grade », produite par Ferroglobe et Elkem.
Pour la fabrication des plaquettes de silicium destinées au photovoltaïque et à la microélectronique, le polysilicium doit être recristallisé en lingots poly- ou monocristallins. L'état monocristallin est plus difficile à obtenir car les atomes de Si en phase gazeuse doivent être déposés selon une structure très ordonnée. Cette étape est réalisée à partir du polysilicium par les méthodes de Czochralski ou de la zone fondue flottante. Les cellules photovoltaïques au silicium monocristallin offrent un meilleur rendement (moyenne 2018 de 17,9 % selon IHS Markit 2019) par rapport aux cellules fabriquées à partir de silicium polycristallin (moyenne 2018 de 16,7 %). Pour la microélectronique, l'état monocristallin est indispensable. Ces méthodes demandent un apport en électricité très important et très stable.

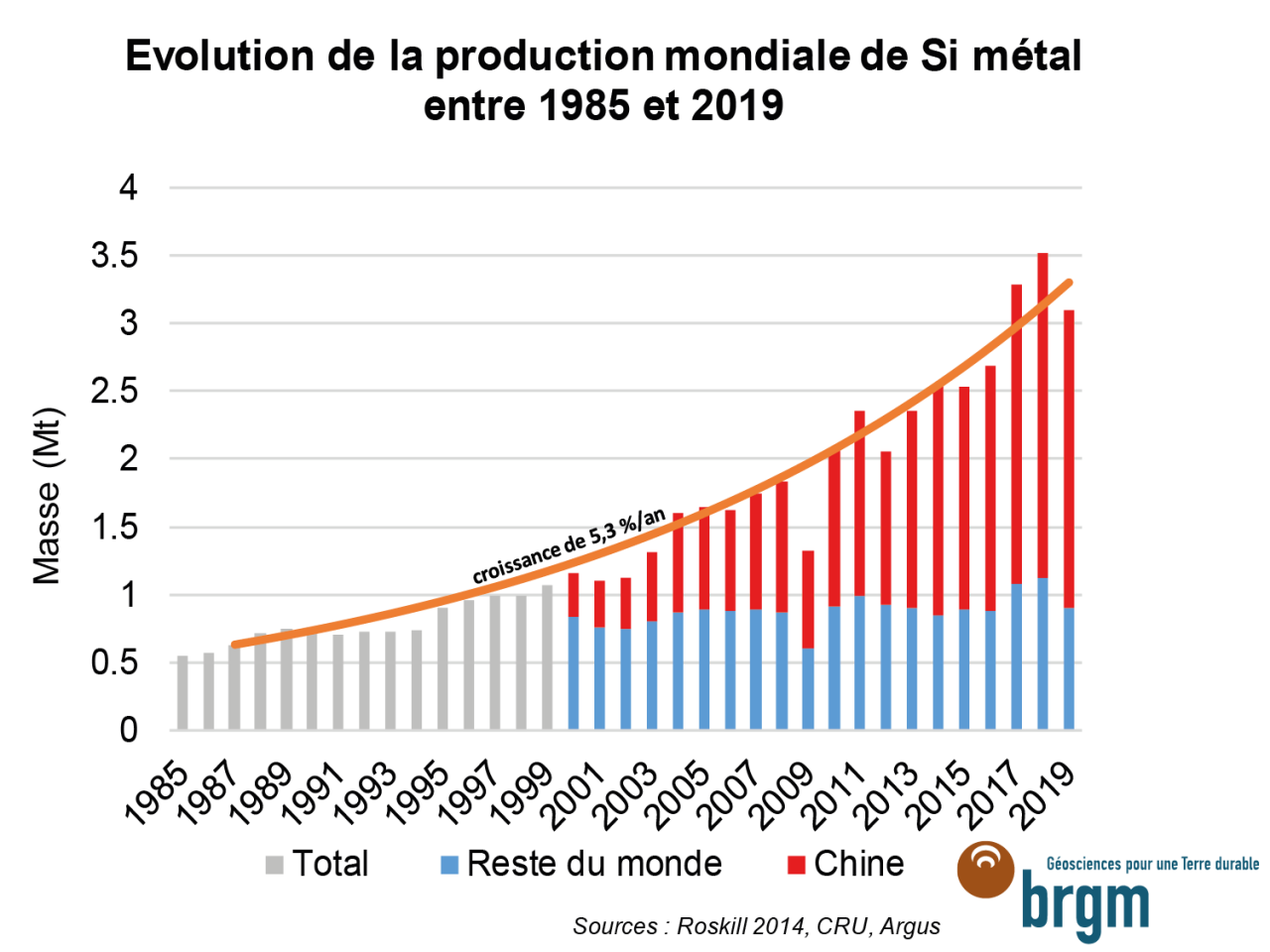
Evolution de la production mondiale de Si métal entre 1985 et 2019
© BRGM, d'après Roskill 2014, CRU, Argus
L’offre écrasante de la Chine
De grandes surcapacités de production
La production de silicium métal a suivi une croissance relativement stable sur les 30 dernières années, à près de 5 %/an. Il semble cependant que la production ait reculé en 2019, à environ 3,1 Mt (BRGM). La Chine est depuis plusieurs décennies le plus gros producteur de silicium métal avec 2,2 Mt en 2019 selon Argus, soit 71 % de la production mondiale. Les autres principaux producteurs sont le Brésil (200 kt), la Norvège (170 kt), les États-Unis (135 kt), et la France (100 kt).
Entre 2000 et 2019, la part de la Chine dans la production mondiale de silicium métal a augmenté de 30 % à 71 %, la production des acteurs historiques étant restée stable. Sur la période 2000-2007, la Chine a massivement installé de nouvelles capacités de production grâce à la présence locale de toutes les matières premières (quartz, électrodes, charbon, bois) et à un accroissement de la production d’électricité. Elle a ainsi pu satisfaire une demande intérieure de silicium métal en pleine expansion (+250 % entre 2000 et 2007) tout en répondant à une demande croissante hors-Chine. La part des exportations a ainsi été maintenue à environ 80 % durant cette période. Par la suite, ce taux d’exportation est redescendu à mesure que les exportations de produits de plus haute valeur ajoutée (voitures, silicones, cellules photovoltaïques) ont été favorisés. Ce taux était de 43 % en 2018.
En 2019, les capacités mondiales de production de silicium métal étaient d’environ 6 Mt, dont plus de 80 % se situaient en Chine. Elles représentaient donc plus du double de la demande mondiale. Ces surcapacités vertigineuses ne sont pas l’apanage du marché du silicium métal, on les retrouve en effet dans toute l’industrie lourde chinoise, en particulier sur les marchés de l’acier, de l’aluminium, du charbon et du ciment. Celles-ci permettent aux producteurs chinois d’optimiser les prix de vente, en s’adaptant rapidement aux évolutions de la demande et aux cours des matières premières. Dans le cas du silicium métal, les surcapacités sont accentuées par une production en grande partie intermittente. En effet, les usines de production, majoritairement situées dans le sud du pays (en particulier Yunnan, Sichuan, et Guizhou), sont alimentées en électricité par des centrales hydroélectriques. Elles produisent donc préférentiellement lors de la saison des pluies—au printemps—lorsque l'électricité est moins chère. Les installations ont de fait un plus faible facteur de charge5 et un agenda de production moins prévisible dû au caractère aléatoire des précipitations. En 2018, le taux d’utilisation moyen des usines de production du Yunnan était de 46 %, selon Shanghai Metals Market.
Au cours de la décennie 2010-2020, de nouvelles usines de production ont vu le jour dans le nord de la Chine, tout particulièrement dans la région autonome ouïghoure du Xinjiang où l'électricité à base de charbon est stable et peu chère. A partir de 2015, cette province est devenue la première productrice de silicium métal devant le Yunnan, à la faveur d’un développement économique massif, facilité par ses frontières communes avec huit pays, ainsi qu'un accès privilégié à la « nouvelle route de la soie ». En 2019, la province du Xinjiang a produit plus d’1 Mt de Si métal, devant le Yunnan, 480 kt, et le Sichuan, 340 kt. Mais ce classement pourrait à nouveau évoluer après 2020, le numéro un chinois du silicium métal Hoshine Silicon ayant annoncé la construction d’un méga-projet d’une capacité de 800 kt dans le Yunnan. Ces nouvelles usines ne réjouissent guère les producteurs occidentaux, qui voient là autant de surcapacités pesant sur les prix.
La pression des prix bas
Le marché du silicium métal est reconnu comme étant cyclique. Lorsque les prix baissent et se rapprochent des coûts de production, le marché se réorganise et les acteurs tendent à limiter leur production. Le prix du silicium métal est moins élevé en Chine mais également moins volatile qu'en Europe et aux États-Unis.
Au cours des années 2018 et 2019, les perturbations sur le marché de l’acier et de l’aluminium [7] dues à un ralentissement économique mondial ont causé une forte chute des prix. Ces chutes ont été appuyées par les tensions commerciales entre les États-Unis et la Chine et les nouvelles capacités de production chinoises. De nombreuses usines ont stoppé leur production en Europe et en Amérique du Nord. En dépit de taxes à l’importation depuis la Chine de 16,8 % en Europe, de 139 % aux États-Unis, et de 235 % au Canada, sur le silicium métal de qualité inférieure à 99,99 %, les acteurs européens et américains du silicium métal comme Ferroglobe ont subi de lourdes pertes de revenu.
Selon plusieurs analystes comme Alloyconsult, l'année 2020 devait sonner le retour à la prospérité pour les producteurs de silicium métal. Mais la pandémie COVID-19 a sensiblement perturbé l'offre chinoise en début d'année, et risque bien d'impacter la demande mondiale au cours de l'année 2020 et au-delà.
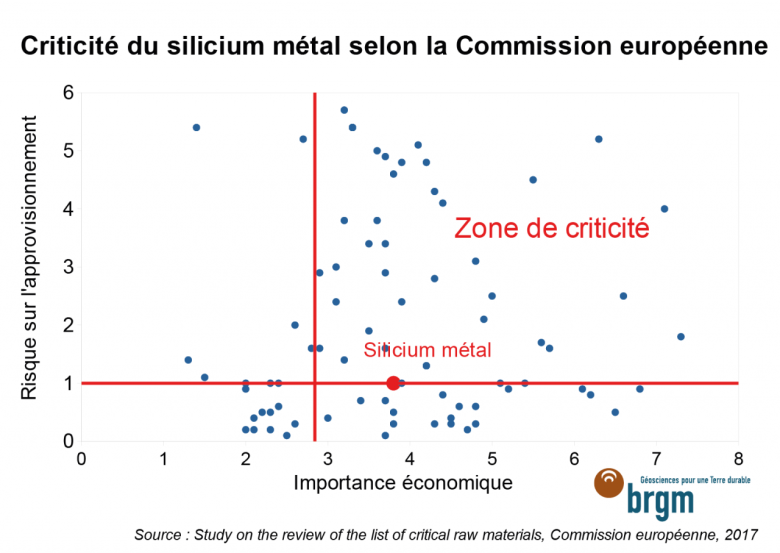
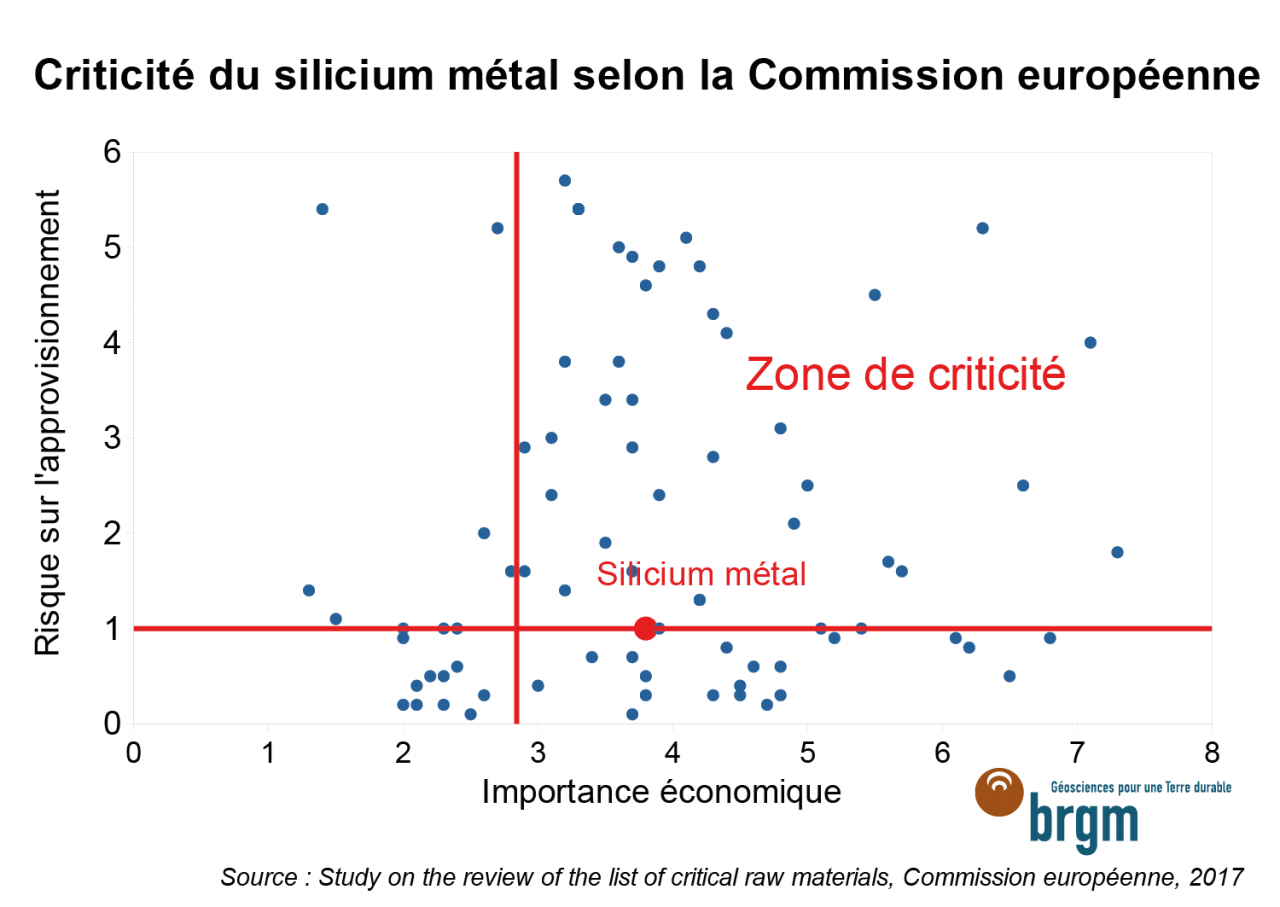
Criticité du silicium métal selon la Commission européenne
Source : Study on the review of the list of criticial raw materials, Commission Européenne, 2017
Une criticité à géométrie variable
Criticités européenne et française
Le silicium métal a été classé parmi les matières premières critiques par la Commission européenne en 2014 et 2017 [8]. Les principaux déterminants invoqués ont été la forte concentration du marché en Chine ainsi que l'importance économique du silicium métal pour l'économie européenne (secteurs aluminium, silicones, solaire, et microélectronique).
A l'échelle de la France, le BRGM a réalisé la première édition de la fiche de criticité du silicium métal en 2019 [10] en faisant une synthèse des différents enjeux sur l’amont de la chaîne et leurs perspectives d’évolution. Ont été reconnus l'importance économique du silicium métal pour l'industrie française ainsi qu'un risque modéré sur les approvisionnements. Rappelons que la France produit du silicium métal sur son sol et dispose de ressources en quartz de haute pureté.
Dans les deux études à l'échelle européenne et française, les marchés de produits contenant du silicium métal n'ont pas été pris en compte. En effet, ces études se sont focalisées sur l'extraction et la première transformation. Elles ne permettaient donc pas de révéler l’importance économique et le risque de pénurie des produits intermédiaires et finaux fabriqués à partir de cette substance. Pour réaliser cette tâche, il faut recourir à une analyse complète de l'ensemble des chaînes de transformation, en considérant les marchés associés à chaque étape. Un tel exercice a été entrepris par le Ministère de la transition écologique et solidaire avec l’appui du BRGM et du CEA dans le cadre du plan de programmation des ressources minérales de la transition bas carbone6. Cet exercice a permis de mettre en évidence plusieurs maillons critiques sur la chaîne de transformation du silicium métal. Parmi ceux-ci, l'étape de production du polysilicium s'est révélée particulièrement stratégique.
Le polysilicium : une substance stratégique
Les filières solaire et microélectronique représentent toutes deux des secteurs stratégiques pour le développement économique des pays industrialisés : la filière solaire est attendue comme une voie majeure pour la décarbonation du système énergétique mondial, alors que les circuits intégrés, principalement basés sur des semiconducteurs au silicium monocristallin, sont la brique élémentaire du numérique. Ces deux filières se partageaient le marché du polysilicium à plus de 90 % pour le solaire et moins de 10 % pour la microélectronique en 2019.
Le polysilicium est principalement produit par le procédé Siemens, bien que la technique de production en lit fluidisé soit de plus en plus utilisée4. Ces procédés font appel à d’imposantes usines très capitalistiques et fortement consommatrices de produits chimiques et d’énergie. A cet égard, il n’existe qu’une poignée de producteurs, la plupart situés en Asie. On peut mentionner les chinois GCL (1er), Xinte Energy (4ème), Daqo (5ème), et Yongxiang (6ème), et le sud-coréen OCI (3ème). En Europe, l'allemand Wacker est le seul producteur de polysilicium de qualité SoG (solaire) et EG (électronique). Comme GCL, il a réalisé 14 % de la production mondiale de polysilicium en 2018, soit environ 60 kt, ce qui le place dans le duo de tête mondial sur ce marché.
La production mondiale de polysilicium 2018 a stagné à environ 450 kt selon Research and Markets en raison d'un coup d'arrêt sur les subventions à l’installation des panneaux solaires en Chine courant 2018 (installation de 44 GW en 2018 contre 53 GW en 2017). La demande croissante en produits de plus haute efficacité énergétique a poussé les fabricants de cellules à se tourner vers les plus hauts rendements. On observe ainsi depuis 2017 un fort regain d'intérêt pour les modules photovoltaïques au silicium monocristallin, alors que les modules au silicium polycristallin étaient encore majoritaires en 2018. La compagnie chinoise Daqo a par exemple annoncé le doublement de ses capacités à 70 kt en 2019, avec une extension dans la province du Xinjiang. Elle prévoit que 80 % des cellules photovoltaïques dans le monde seront fabriquées à partir de silicium monocristallin en 2021. Cet engouement pour le silicium monocristallin est intervenu dans un contexte d'accroissement de capacité et de prix historiquement bas, forçant l'amont de la filière solaire à monter en qualité afin de rester compétitif. Un phénomène similaire s'était produit en 2011, alors que le prix du polysilicium—en forte hausse depuis 2005— s'apprêtait à chuter brutalement. Les espoirs des acteurs ayant parié sur le développement de cellules moins chères et moins performantes, telles que celles basées sur le silicium de qualité UMG, avaient alors été douchés.
En 2019, le kilogramme de polysilicium SoG chinois s'est vendu à un minimum historique de près de 7 US$ selon PVInsights, alors qu'il valait encore 15 US$ en 2017, et près de 70 US$ fin 2010. Si cette chute des prix a largement entamé les marges des producteurs chinois, elle a forcé plusieurs producteurs hors-Chine à stopper leur production. Aux États-Unis, les tensions commerciales avec la Chine se sont ajoutées à cela, empêchant les trois producteurs locaux que sont Hemlock Semiconductor, Rec Silicon et Wacker d'exporter leurs matériaux en Chine, partenaire qui absorbe en temps normal plus de 90 % du polysilicium mondial. Le contexte 2020 est donc une guerre des prix, sur laquelle viennent s'ajouter les impacts de la pandémie COVID19.
Le marché du polysilicium de qualité électronique est petit et opaque. Il fournit pourtant le silicium nécessaire aux dizaines de milliards d'appareils électroniques en utilisation. Pour ce secteur de pointe le polysilicium est purifié à l'extrême puis recristallisé en monosilicium. Ce qui a tempéré l'expansion de ce marché, malgré la très forte augmentation du nombre d'appareils utilisés, a été la miniaturisation des composants électroniques. Ainsi, en 2019, certaines parties des semiconducteurs atteignaient des tailles inférieures à 10 nm (nanomètre) ; et les « Big Three » des semiconducteurs que sont TSMC (Taïwan), Intel (États-Unis), et Samsung (Corée du Sud) préparaient activement les futures générations de semiconducteurs avec des tailles envisagées de 5 nm voire 3 nm7.
Une empreinte environnementale à considérer
La production et la transformation du silicium métal sont fortement tributaires d'un apport d'électricité important et stable. Selon Takiguchi [11], la production de silicium MG à partir de quartz demanderait en moyenne 11 MWh/t Si MG3. L'affinage du silicium en polysilicium consommerait 150 MWh/t. La transformation du polysilicium en lingot monocristallin consommerait 31 MWh/t. Enfin, la découpe des plaquettes consommerait 42,5 MWh/t. En fonction des procédés utilisés, ces valeurs peuvent varier du simple au double.
L’empreinte carbone de la production et de la transformation du silicium métal dépend beaucoup de la source d’électricité utilisée (hydraulique, nucléaire, ou charbon). Il y a donc un fort enjeu à réaliser les étapes de transformation et d'affinage à partir d'un mix électrique le plus décarboné possible. Ferroglobe indique des émissions directes et indirectes moyennes de 4 t CO2,eq/t Si MG en Europe et de 15 t CO2,eq/t Si MG dans le nord de la Chine à cause d’une électricité provenant majoritairement de centrales à charbon. La production de polysilicium SoG, quant à elle, produirait en moyenne 141 kg CO2,eq/kg Si SoG en Chine contre 87 kg CO2,eq/kg Si SoG en Allemagne selon Nugent et Sovacool [10]. Selon ces auteurs, près de 70 % des émissions de gaz à effet de serre générées par une installation photovoltaïque proviendraient de la phase de production de polysilicium en raison de sa très forte consommation d'électricité. Le contenu carbone d'un panneau photovoltaïque est donc directement dépendant du mix électrique utilisé pour produire le polysilicium.
Du point de vue de la consommation matière, il faut 2,8 t de quartz soit 1,3 t de Si contenu pour produire 1 t de Si MG. Selon Roskill, il faudrait environ 1,5 t de Si MG pour produire 1 t de poly-Si SoG, et 1,7 t de poly-Si SoG pour produire 1 t de mono-Si SoG. Ceci donne un rendement d'environ 30 % pour l'obtention d'un lingot de silicium monocristallin. Les 70 % restants étant transformés en sous-produits (p. ex. fumée de silice, tétrachlorosilane, etc.) ou en déchets. Certaines chutes de production peuvent être éventuellement réutilisées. C'est le cas de certaines sections de lingots de la filière électronique qui sont traitées dans la filière solaire.
Une fois le lingot de silicium cristallin obtenu, il est scié par des fils diamantés en plaquettes de quelques microns d'épaisseur. Ceci génère la perte de plus de 40 % du lingot sous forme d'un mélange liquide-poussière de silicium appelées « kerf », difficilement valorisable. Les étapes suivantes de traitement génèrent des pertes supplémentaires d'autant plus grandes que la performance du produit final est élevée. Cependant, l'évolution à la hausse observée du taux de résidus de production ne traduit pas une une perte d'efficacité. Au contraire, elle est la nécessaire conséquence d'un gain plus important sur l'intensité matière et la performance des produits. Ainsi, on a observé une réduction de moitié de la quantité de silicium par cellule solaire entre les années 2004 (16 g/Wc) et 2009 (8 g/Wc) selon le Fraunhofer ISE [12]. En 2020, cette quantité avait encore réduit de plus de la moitié, à 3,5 g/Wc. Si l'intensité matière des produits diminue, la consommation de silicium dans chaque secteur augmente en raison d'une croissance plus rapide de la consommation des produits.
L'affinage du polysilicium et la fabrication des produits demandent également un usage intensif de substances chimiques de haute pureté. Cependant, peu nombreuses sont les analyses de cycle de vie qui prennent en compte l'ensemble de ces substances, au regard du grand nombre d'étapes, de la complexité des procédés, et du peu de données disponibles.
Une substance très peu recyclée
Le silicium métal n'est quasiment pas recyclé en boucle longue, c'est-à-dire par le traitement de produits arrivant en fin de vie. Dans la filière du recyclage de l'aluminium, il peut s'agir d'un recyclage non fonctionnel, où les atomes de Si piégés dans la masse sont dilués dans d'autres alliages. Dans la filière silicones, il est très difficile de récupérer le silicium, bien que le recyclage non fonctionnel puisse être également envisagé. Pour les panneaux photovoltaïques, certains acteurs du recyclage tels que RoSi Solar effectuent des recherches et expérimentent des pilotes industriels pour démontrer la possibilité de revalorisation du polysilicium. Au-delà de la difficulté de récupérer le silicium dans les composants, le faible coût du silicium, les faibles quantités collectées, et le coût élevé des procédés rendent cette récupération encore peu rentable en 2020.
Conclusion
Le silicium métal est souvent considéré comme incontournable pour répondre aux objectifs de transition vers une économie bas-carbone. Ses usages offrent de nombreuses possibilités d’accroissement de l’efficacité énergétique et de réduction des émissions de gaz à effet de serre dans les secteurs des transports, de l’énergie et du numérique. Dans le cadre de la décarbonation des activités industrielles, de nombreux travaux de recherche et analyses économiques montrent que la consommation de silicium métal est amenée à croître fortement8.
Les multiples marchés du silicium métal, correspondant chacun à une étape de transformation et à un usage dédié, répondent à des jeux d'acteurs complexes. Comme pour beaucoup d’autres métaux, la Chine s’est imposée comme l’acteur central, véritable rouleau compresseur industriel et politique. Contrôlant la quasi totalité des étapes de transformation en produits de haute valeur ajoutée, elle est en passe de résoudre certains points faibles tels que sa forte empreinte carbone, sa dépendance aux importations de polysilicium de haute pureté, et son retard dans la course aux semiconducteurs.
Abondant mais stratégique, peu cher mais énergivore, peu substituable et peu recyclé, le silicium métal possède des caractéristiques de criticité pouvant donner lieu à des analyses divergentes. En cela, il convient de considérer l'ensemble du tissu industriel entourant la filière silicium métal pour en apprécier les éléments de criticité. Il s'avère que ces éléments ne portent pas uniquement sur l'amont de la chaîne de transformation, mais également sur des étapes intermédiaires faisant appel à des procédés, des équipements, et des acteurs aussi spécialisés qu'indispensables. Il faut également tenir compte de l'évolution des cadres réglementaires, favorisant dans de nombreux pays les projets industriels ayant une plus faible empreinte environnementale.
Les tensions commerciales et la compétition industrielle modifient très rapidement les marchés et les rapports de force entre acteurs. Elles favorisent parfois les alternatives techniques et le recyclage, à l’instar du développement continu de la filière des cellules photovoltaïques au tellurure de cadmium (CdTe) de l’américain First Solar. Mais, si le contexte de prix bas suggère une grande disponibilité des ressources, il cache en réalité un phénomène de concentration du marché vers ceux qui peuvent encore produire aux coûts les plus bas. A l'échelle nationale, une plus grande dépendance aux importations se traduit bien souvent par une plus grande exposition au risque de pénurie. Dans cette géopolitique mouvante, l'Europe pourrait voir sa souveraineté s'éroder si elle ne maintenait pas son savoir-faire industriel, associé à un certain contrôle de ses approvisionnements, que ceux-ci proviennent de ressources primaires (extraction) ou secondaires (réutilisation et recyclage).
Antoine Boubault, BRGM
Notes de texte
1 Les principaux constituants du globe terrestre sont l’oxygène (33 %), le fer (33 %), et le silicium (15 %). Les principaux constituants de la croûte terrestre sont l’oxygène (49 %), le silicium (28 %), et l’aluminium (10 %).
2 Afin d'illustrer ce niveau de pureté extrême : si la Tour Eiffel était intégralement faite de polysilicium 11N, la quantité d'impuretés contenue serait de l'ordre de grandeur de la masse d'une goutte de pluie.
3 A titre de comparaison, 12 MWh correspond à l’énergie thermique récupérable dans 1 tonnes de pétrole.
4 L'affinage en réacteur à lit fluidisé peut être réalisé en continu et possède un meilleur rendement énergétique. Le procédé Siemens offre un meilleur contrôle de la qualité du produit. La voie métallurgique permet de produire du polysilicium de qualité 6N à moindre coût par rapport à la voie chimique.
5 Le facteur de charge d’une installation de production d’électricité est le ratio entre l’électricité moyenne produite sur une année et l’électricité qu’elle produirait si elle fonctionnait à pleine capacité.
6 Dans le cadre de l'action 5 de la feuille de route sur l'économie circulaire d’avril 2018, la secrétaire d’État à l’écologie, Brune Poirson, a lancé le 22 février 2019 les travaux d’élaboration d’un plan de programmation des ressources minérales de la transition bas carbone. Ce plan, inscrit dans la continuité du plan ressources pour la France de juillet 2018, sera accompagné d'une « politique industrielle ambitieuse de valorisation du stock de matières, en particulier pour les métaux critiques, contenues dans les déchets ». Il portera en particulier sur quatre familles de technologies bas-carbone : le photovoltaïque, le stockage stationnaire et les réseaux (y compris réseaux intelligents), la mobilité bas-carbone et l’éolien.
7 3 nm représente la taille des plus petits éléments du semiconducteur. Cela correspond à l'épaisseur d'un empilement de 25 atomes de Si.
8 Le projet SURFER (2016-2020), porté par le BRGM, le CNRS, et financé par l’ADEME, vise à estimer les besoins en ressources minérales dans des scénarios de transition vers une économie bas-carbone. Le silicium métal est une des substances sélectionnées dans cette étude.
Sources
[1] IRP-UNEP, « Global resources outlook 2019 ». 2019.
[2] P. Marteau, « Mémento silice industrielle », Mémento RP-66167-FR. Consulté le: 22/07/2019. [En ligne]. Disponible sur: http://infoterre.brgm.fr/rapports//RP-66167-FR.pdf.
[3] C. Bonnet, « La silice industrielle », Guide Mines Carr., p. 399‑402, 2010.
[4] Ferropem, « Dire d’expert ». 2019.
[5] I. Kero, S. Grådahl, et G. Tranell, « Airborne Emissions from Si/FeSi Production », JOM, vol. 69, no 2, p. 365‑380, févr. 2017, doi: 10.1007/s11837-016-2149-x.
[6] « Silicium », L’Élémentarium. https://www.lelementarium.fr/element/silicium/ (consulté le mai 26, 2020).
[7] Minéralinfo, « Retour à la normale du marché de l‘alumine, après une année 2018 turbulente », avr. 2019, [En ligne]. Disponible sur lien
[8] European Commission, Study on the review of the list of critical raw materials: final report. 2017.
[9] BRGM, « Fiche de criticité - Silicium métal », août 2019. (consulté le sept. 03, 2019).
[10] D. Nugent et B. K. Sovacool, « Assessing the lifecycle greenhouse gas emissions from solar PV and wind energy: A critical meta-survey », Energy Policy, vol. 65, p. 229‑244, févr. 2014, doi: 10.1016/j.enpol.2013.10.048.
[11] H. Takiguchi, « Global Flow Analysis of Crystalline Silicon », Cryst. Silicon - Prop. Uses, juill. 2011, doi: 10.5772/23573.
[12] Fraunhofer Ise, « Photovoltaics Report », 2019.