Cet article dresse un état des lieux des principaux enjeux technologiques liés au recyclage des véhicules hybrides, aux Etats-Unis, au Japon et en Europe à fin 2014, avec un focus particulier sur le cas du recyclage des batteries.
LES VEHICULES HYBRIDES ELECTRIQUES
Principe
La motorisation hybride électrique est l’association d’un moteur électrique et d’un moteur thermique dans une même voiture. Cette hybridation peut être en parallèle, en série, ou être une association des deux configurations.
Hybridation série : les moteurs thermiques et électriques sont totalement dissociés. Le moteur thermique alimente un générateur électrique. Celui-ci fournit la puissance au moteur électrique, qui assure seul la propulsion des roues, ainsi qu’à la batterie de stockage, qui récupère également l’énergie dégagée lors des freinages et des décélérations du véhicule.
Hybridation parallèle : l’énergie de traction peut aussi bien provenir du moteur thermique que du moteur électrique. La batterie alimente le moteur électrique, mais celui-ci peut également fonctionner en tant que générateur pour recharger la batterie, celle-ci stockant également l’énergie dégagée lors des décélérations.
Hybridation série/parallèle : sélection de l’utilisation du moteur, électrique ou thermique, selon les conditions routières. Le chargement du générateur lui permet également de recharger la batterie en permanence.
Un véhicule hybride présente un meilleur rendement énergétique qu’un véhicule thermique, du fait que le moteur électrique assume le démarrage du véhicule - jusqu’à 30 à 50 km/h environ, et que la batterie peut stocker l’excédent d’énergie produit par le moteur thermique sous forme électrique et récupérer l’énergie dissipée lors des freinages.
Production de véhicules hybrides
Environ 9 millions de véhicules hybrides sont en circulation dans le monde en 2014, dont plus de 7 millions produits par Toyota Motor Company. Les principaux marchés actuels sont les Etats-Unis et le Japon, avec une croissance exponentielle dans ces deux pays depuis 2005. Aux Etats-Unis, les ventes de véhicules hybrides qui se chiffraient à moins 10 000 en 2000 et à 35 000 en 2002, ont atteint 3 millions en octobre 2013, soit environ 3 % des ventes [2]. Au Japon, une politique de soutien intensive aux véhicules hybrides, associant primes à la reprise de véhicules polluants, allègement des taxes sur les véhicules décarbonés et taxe sur les carburants, a entraîné un triplement du parc hybride entre 2008 et 2009. En 2013, environ 3,87 millions de véhicules hybrides étaient en circulation au Japon, représentant 5 % du parc total, et les nouvelles ventes représentaient 20 % du marché en 2013 [3]. De son côté, le parc européen ne totalisait que 0,65 millions d’unités en août 2013, soit 0,08 % du parc total et, sur les 12 008 247 véhicules vendus dans l’UE-27 en 2012, les véhicules hybrides n’en représentaient que 1,1 % [4]. A l’échelle de la France, ce taux atteint 1,3 %, mais un Plan National de Développement des Véhicules Electriques et Hybrides Rechargeables a été lancé en 2012, avec l’objectif de créer un parc de deux millions de véhicules à l’horizon 2020, notamment par un soutien à la recherche et la création d’une filière française de fabrication de batteries.
RECYCLAGE DES VEHICULES HYBRIDES
Les premières commercialisations de véhicules hybrides non rechargeables datent du début des années 2000. La durée de vie de ces véhicules est de l’ordre de 10 à 15 ans. Les premiers véhicules usagés commencent ainsi à arriver sur le marché de la réutilisation et du recyclage.
Le recyclage des véhicules hybrides s’inscrit dans le cadre législatif des VHU conventionnels. En Europe, le taux de réutilisation et de valorisation (en masse) des matériaux d’un VHU doit atteindre 95 % d’ici au 1er janvier 2015 [5]. En 2012, 87 % des matériaux des véhicules usagés auraient été valorisés [6]. Au Japon, 70 % des RBA (Résidus de Broyage d’Automobile) et 85 % des airbags doivent être recyclés à partir de 2015 [7]. Aux Etats-Unis, le Resource Conservation Recovery Act ne fixe pas d’objectifs, mais environ 95 % des VHU sont actuellement recyclés, avec un taux de recyclage de 80 % [8].
Le recyclage des VHU hybrides présente des spécificités liées à la batterie et au moteur électrique. En effet, ce système de propulsion représente une augmentation de 200 à 400 kg par rapport à une propulsion purement thermique. Ceci, conjugué à l’intensification des pressions règlementaires pour diminuer les émissions de CO2 liées aux transports et réduire la consommation d’énergie des véhicules aussi bien en Europe [9], aux Etats-Unis [10] qu’au Japon [11], mène à une “chasse au poids” dans ces véhicules.
Recyclage du véhicule hybride hors moteur et batterie
Les véhicules hybrides incorporent davantage de plastiques composites, contenant des fibres de carbone, tandis que leur part de métaux ferreux pondéreux est en net recul en faveur de métaux plus légers tels que l’aluminium par exemple. A titre d’exemple, la nouvelle BMW i3 présentée à la 14ème édition de l’IARC (International Automobile Recycling Congress) en 2014 contient 31 % en poids de polymères et seulement 50 % de métaux, contre 75 % pour un véhicule traditionnel [12]. En parallèle, la part de plastiques recyclés entrant dans la composition de nouveaux véhicules augmente. Le constructeur Renault affirme ainsi avoir utilisé 45 Mt de plastiques recyclés pour la fabrication de ses nouveaux modèles en 2012, soit une augmentation de leur proportion moyenne par véhicule de 5 % en 1998 à 17 % en 2012. Une carrosserie ainsi allégée peut impacter négativement le modèle économique du recyclage des véhicules, avec moins de métaux à récupérer et plus de matières complexes à gérer. Toutefois, certains recycleurs soulignent aussi le fait que les métaux légers de remplacement sont aussi ceux qui se vendent le plus cher sur les marchés des matières premières recyclées [13].
Du point de vue technique, les premiers procédés développés pour le recyclage spécifique des véhicules hybrides sont similaires à ceux opérés pour les VHU conventionnels, une fois les véhicules débarrassés de leur batterie et de leur moteur électrique. Dans le procédé développé par le centre Recycar du groupe Comet, la batterie est extraite manuellement et envoyée chez un recycleur spécialisé, puis la boîte pont à aimants permanents est retirée, et le véhicule suit alors un traitement classique de broyage, séparation de la ferraille dans les résidus de broyage au moyen de séparations magnétiques, puis post-broyage sur les flux ainsi épurés et séparation du flux de sortie en métaux non ferreux, plastiques (PE, PP, ABS, PS) et matières minérales [14]. Au terme de ce procédé, Comet déclare pouvoir recycler un VHU conventionnel ou électrique de la même façon et atteindre un taux de recyclage de 96 %, soit un point de plus que le seuil règlementaire de 95 % de réutilisation et de valorisation des VHU.
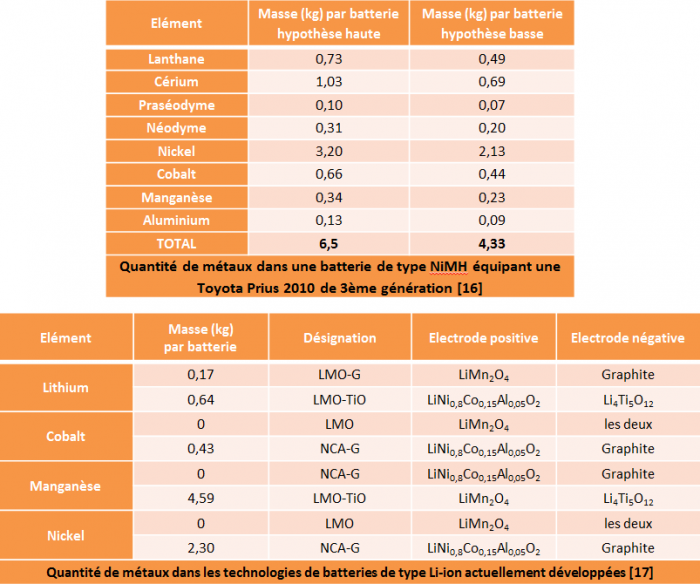
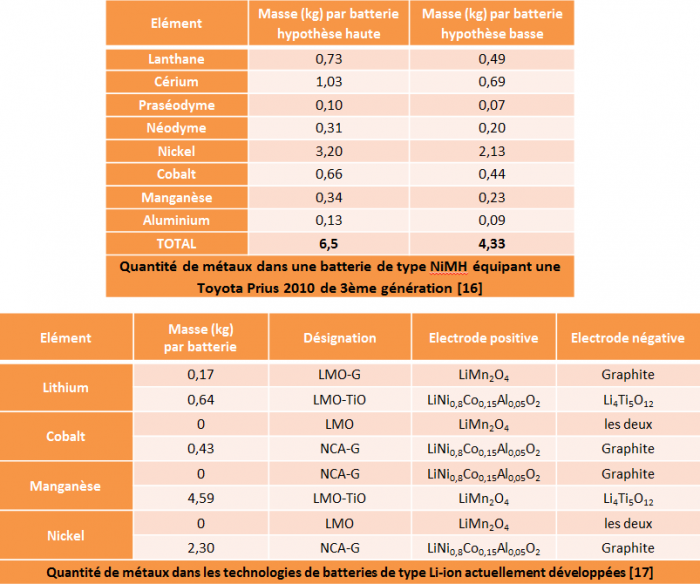
Quantité de métaux dans les technologies de batteries
© BRGM, US Department of Energy, Gaines et al. (2009)
Recyclage des batteries
La collecte et le recyclage des batteries industrielles en Europe sont règlementés par la Directive Européenne 2006/66/CE sur les piles et accumulateurs entrée en vigueur le 26 septembre 2006 [15]. Bien que la Directive ne spécifie pas les objectifs de collecte pour les batteries industrielles, depuis septembre 2011, l’efficacité du recyclage doit atteindre un minimum de 50 % du poids collecté. Au-delà de ces aspects règlementaires, trouver un exutoire pour les batteries des véhicules hybrides peut également être une opération rentable selon la nature de la batterie employée.
- Les différents types de batteries
La majorité des batteries pour véhicules hybrides est soit de type NiMH (pour nickel-hydrure métallique), soit de type Lithium-ion. Les trois principaux composants d’une batterie sont l’électrode positive, l’électrode négative et l’électrolyte.
Batterie NiMH pour les véhicules hybrides : l’électrode positive est formée d’oxyhydoxyde de nickel NiO(OH). L’électrode négative est un composé intermétallique, très majoritairement de type AB5, où A est un mélange de terres rares dont le lanthane (La), le cérium (Ce), le néodyme (Nd) et praséodyme (Pr) et B est du nickel, du cobalt ou du manganèse. L’électrolyte est une solution d’hydroxyde de potassium.
Batterie Lithium-ion pour les véhicules hybrides : les électrodes positives utilisées sont principalement de trois types : sous forme d’un oxyde stratifié (technologies “NCA” pour Nickel-Manganèse-Aluminium LiNi0,8Co0,15Al0,05O2 et “NCM” LiNi1/3Co1/3Mn1/3O2), d’un polyanion (technologie “LFP” pour Lithium-Fer-Phosphate LiFePO4), ou d’un spinelle (technologie “LMO” pour Lithium-Manganèse-Oxyde LiMn2O4). L’électrode négative est majoritairement du graphite, mais une technologie alternative, mise sur le marché en 2008 par Toshiba, repose sur du titanate de lithium (technologie “LTO” pour Li4Ti5O12). Enfin, l’électrolyte est un solvant organique, généralement de l’éthylène carbonate, du diméthylcarbonate ou du diéthylcarbonate, contenant des complexes inorganiques de lithium tels que le lithium hexafluorophosphate (LiPF6), hexafluoroarsenate (LiAsF6), perchlorate (LiClO4), tetrafluoroborate (LiBF4) et triflate (LiCF3SO3). L’ensemble des électrodes et de l’électrolyte est placé entre deux collecteurs de courant généralement composés d’aluminium et de cuivre.
En 2010, les batteries NiMH constituaient le standard pour équiper les voitures hybrides. En effet, malgré des performances en retrait par rapport aux batteries à base de lithium, leur technologie est éprouvée, elles sont moins onéreuses, elles gardent l'avantage de bien supporter de forts courants de charge et de décharge, et elles sont beaucoup plus sûres en cas de surchauffe. Toutefois, du fait de leur plus grande énergie spécifique, de leur plus longue durée de vie, et des efforts de R&D actuels, les batteries Li-ion devrait progressivement capter des parts de marché de plus en plus importantes. En 2012, Toyota a ainsi équipé son modèle de Prius hybride rechargeable de batteries de technologie Li-ion.
- Quantité de métaux présents dans les batteries
Le ministère de l’énergie américain (US Departement of Energy – DOE) évalue [16] les quantités de métaux dans une batterie NiMH dont la capacité et la composition chimique fournissent une puissance nominale et une tension analogue à celle d’une Toyota Prius de troisième génération, constituée de 28 modules de 1040 g chacun, en considérant deux hypothèses, l’une haute, correspondant aux quantités actuelles, et l’autre basse, correspondant à une technologie plus économe attendue dans les années à venir. De façon similaire, l’Argonne National Laboratory estime les quantités de métaux dans les technologies de batteries lithium-ion en cours de développement et assurant une autonomie de 7 km environ [17]. Enfin, un récent rapport du Mineta National Transit Research Consortium estime qu’entre 1,3 et 6,7 millions de batteries de véhicules hybrides arriveront en fin de vie d’ici 2035 aux Etats-Unis [18].
- Les procédés de recyclage
Pour une même nature chimique, les batteries ne présentent pas de caractéristiques standardisées. Elles peuvent différer par leur nature chimique, leur taille et la configuration de leurs électrodes. La technologie de recyclage doit donc être suffisamment robuste pour traiter des batteries de natures chimiques différentes, ce qui est le cas des procédés reposant sur la voie pyrométallurgique.
Recyclage par pyrométallurgie
En 2014, la méthode de recyclage des batteries non hybrides mise en œuvre à échelle industrielle est fondée sur une étape de pyrométallurgie des batteries, qui mène à des alliages fins de cobalt, cuivre, fer, nickel et zinc et à des résidus concentrant les terres rares, l’aluminium, le calcium, le lithium, et le manganèse, suivie d’opérations d’hydrométallurgie pour récupérer successivement le cuivre, puis le zinc et le fer, et enfin le cobalt et le nickel, qui peuvent être utilisés pour reformer les électrodes positives des batteries NiMH ou Li-ion de type NCA (voir figure ci-dessous). Le lithium n’est actuellement pas récupéré. Ce procédé est mis en œuvre par le groupe Umicore.
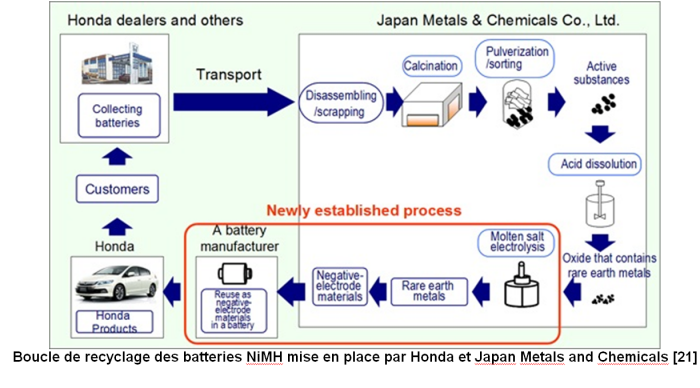
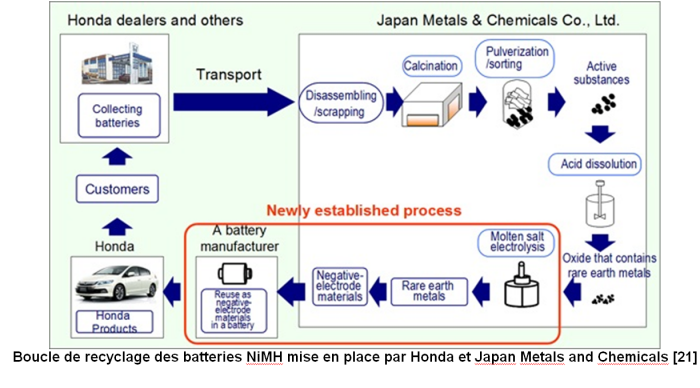
Boucle de recyclage des batteries NiMH mise en place par Honda et Japan Metals and Chemicals
© Gaines et al. (2014)
Dans ce procédé les matières organiques, y compris les électrolytes et les électrodes négatives des batteries Li-ion, servent de combustible. Pour une tonne de batteries entrant dans le procédé de recyclage, l’étape de smelting, comprenant le nettoyage des gaz, consomme 5000 MJ [19]. Les batteries sont désassemblées en Allemagne pour les batteries en Europe, et à Maxton (Caroline du Nord) pour les batteries aux Etats-Unis. Les cellules démantelées sont envoyées sur le pilote industriel à Hoboken en Belgique. Le concentré de terres rares est retraité en France, chez Solvay.
Au Japon, le groupe Honda a signé en 2012 un accord avec Japan Metals and Chemicals [20] pour le développement d’un procédé à haute température permettant la récupération des terres rares des batteries NiMH et leur réutilisation dans des véhicules hybrides. Le procédé de purification repose sur une électrolyse en sels fondus du mélange d’oxydes de terres rares récupérées après dissolution acide des résidus de calcination des batteries. La récupération est de 80 % des terres rares initiales, présentant par ailleurs une pureté supérieure à 99 %, ce qui autorise, selon Honda, leur réemploi comme matériau d’électrode négative dans une batterie NiMH.
Recyclage à basse température
Ce procédé est mis en œuvre par Retriev Technology (anciennement Toxco), société canadienne associée dans une joint-venture avec le principal recycleur de batteries des Etats-Unis, Kinsbursky Brothers Inc. Il repose sur un broyage en deux étapes des batteries afin d’atteindre la maille de libération des plastiques et des métaux, puis la séparation des métaux grossiers des plastiques au moyen de tables à secousses, et de la récupération des fines métalliques par filtration [21]. Pour 907,4 kg de batteries, 227 kg d’un assemblage de cobalt et de cuivre, et 30 kg de Li2CO3. Pour rappel, la batterie Li-ion équipant le modèle Leaf de Nissan pèse environ 200 kg. Le recyclage des batteries NiMH est réalisé par désassemblage manuel, suivi d’un broyage des plastiques, la récupération et la neutralisation de l’électrolyte alcalin, et la récupération des terres rares. Les plaques de nickel sont envoyées dans une fonderie pour former de l’acier [22].
Recyclage par récupération directe
La récupération des composants des batteries a fait l’objet de démonstration pilote sur des batteries Li-ion, mais n’est pas implémentée industriellement. Le procédé requiert un flux d’entrée aussi uniforme en composition que possible. Une première étape consiste à extraire l’électrolyte organique par du CO2 à l’état supercritique pour une réutilisation dans de nouvelles batteries. Par la suite, les composants sont séparés par une série d’opérations physico-chimiques, de flottation, de flottaison et de filtration. Le matériau constituant l’électrode positive peut nécessiter une étape d’enrichissement en lithium avant d’être utilisé pour de nouvelles batteries.
- La rentabilité du recyclage dépend de la technologie de la batterie
Si le recyclage des batteries NiMH présente un intérêt économique du fait de leurs teneurs en nickel, cobalt et en terres rares, plusieurs facteurs freinent toujours le développement du recyclage des batteries Li-ion par des procédés autres que pyrométallurgiques.
En premier lieu, la diversité du type de batteries et de leur agencement en pack, ainsi que la variabilité de la nature chimique de leurs cathodes et anodes, qui sont par ailleurs toujours en amélioration, entraînent une hétérogénéité des flux d’entrée, qui affecte le rendement global du procédé de recyclage. En second lieu, la valeur sur le marché du lithium est faible devant celui du cobalt et du nickel. Ces deux éléments pourraient apporter une valeur au recyclage, mais les études actuelles portant sur le développement de nouvelles chimies de batteries visent à en diminuer les teneurs.
Ces deux déterminants mènent à deux philosophies de recyclage : l’une fondée sur les volumes traités et passant par l’utilisation d’un procédé robuste tel que la pyrométallurgie, et l’autre fondée sur la valeur récupérée et passant par le développement de procédés de recyclage pour chacune des natures chimiques des batteries traitées. Actuellement, la première voie est suivie mais la récupération de l’intégralité des éléments passe par des opérations hydrométallurgiques supplémentaires en sortie de four. Pour être viable, la seconde voie nécessiterait la convergence des matériaux et des designs de batteries ainsi que l’automatisation du tri entre les différents types de batteries. Ce dernier point pourrait passer par l’apposition de code-barres, de puces RFID ou l’utilisation d’un code couleur entre les différents modèles de batteries. Enfin, une option alternative pourrait être de suivre une logique de réemploi partiel, en récupérant les cathodes intactes au lieu de chercher à séparer leurs éléments constitutifs [23].
- Recyclage ou réutilisation?
Le rapport du Mineta National Transit Research Consortium [18] avance que la récupération des composants individuels des batteries Li-ion ne sera pas profitable avant 2035 aux Etats-Unis, et suggère des solutions alternatives telles que le réusinage (remanufacturing) et le réemploi pour d’autres applications (repurposing) des batteries. Cette réflexion est également menée en France par l’ADEME [24].
Le réusinage consiste à changer les cellules de la batterie n’assurant plus la demande en énergie du véhicule. Cette opération implique l’identification des cellules devenues trop faibles, leur désassemblage, et leur remplacement par des cellules nouvelles, provenant par exemple d’autres batteries usagées. Le coût du réusinage est de l’ordre du quart de celui de l’achat d’une batterie neuve [18]. Le réemploi consiste à utiliser la batterie pour une autre application que la propulsion d’un véhicule, telle que le stockage d’énergie. Il peut s’agir de la substitution de groupes électrogènes utilisés dans les réseaux de distribution d’électricité, du lissage de la pointe d’appel de puissance dans les sous-stations des transports ferroviaires, du stockage de l’excès d’énergie produit par les systèmes de production éoliens et solaires, ou encore d’une source d’énergie de secours dans les centres commerciaux, les hôpitaux et les résidences d’habitation [24]. Cette opération nécessite le désassemblage de toutes les cellules de la batterie, leur réassemblage selon une configuration spécifique, et le développement d’un système de commande adéquat.
Pour les batteries au lithium, le potentiel de réutilisation est très important puisque même lorsqu’une batterie ne peut plus assurer la puissance demandée par la voiture, sa capacité énergétique résiduelle est de l’ordre de 80 % de la capacité initiale [25]. Nissan estime ainsi qu’au bout de 10 ans, la batterie de son modèle tout électrique Leaf conserve au moins 70 % de sa capacité initiale. Ceci lui permettrait d’assurer un service de 10 ans comme composant de stockage dans un réseau d’électricité [26].
Au Japon, le Ministère de l’Environnement a inauguré en 2014 la première ferme solaire au monde, d’une capacité de 10 MW, qui utilise 16 batteries Li-ion du modèle Nissan Leaf, dont le rôle est de lisser la production d’énergie [27]. Développée conjointement entre Sumitomo Corporation et Nissan, la ferme est opérationnelle depuis mars 2014 et son efficacité sera testée durant les trois prochaines années. Aux Pays-Bas, une initiative similaire est en cours entre l’Université Technologique d’Eindhoven, l’université des sciences appliquées d’Arnhem et Nijmegen, et Liander NV, le plus gros opérateur de réseau national, sur des batteries de Volkswagen Golf.
- Quelques acteurs majeurs du retraitement des batteries
Les companies automobiles établissent des partenariats avec des fabricants de batteries, des recycleurs et des fabricants de matériel électronique pour développer le marché d’une utilisation post-automobile. A l’heure actuelle, la majorité des batteries récupérées en Europe sont recyclées par le belge Umicore par voie pyrométallurgique, tandis que les batteries nord-américaines sont traitées par la société Kinsbursky Brothers Inc (KBI). Toutefois, Umicore commence à s’implanter aux Etats-Unis, tandis que la Société Nouvelle d’Affinage des Métaux (SNAM) en France développe ses activités de recyclage des batteries à l’échelle européenne, notamment par la signature de plusieurs contrats avec des fabricants de véhicules :
- avec Toyota en 2010, pour la collecte et le recyclage des batteries nickel-hydrure métallique des véhicules hybrides des marques Toyota et Lexus sur le territoire français. Depuis le mois de juin 2011, le contrat a été étendu à tous les pays de l'Union Européenne;
- avec Honda en 2013, pour la collecte et le recyclage des batteries des véhicules hybrides sur le territoire européen auprès des concessionnaires de la marque et des centres VHU;
- avec Volkswagen, en 2014 pour la collecte auprès des Distributeurs des marques du Groupe et des Centres VHU agréés, le démantèlement et le recyclage des batteries NiMH et Li-ion.
En France, à partir des batteries Li-Ion, qui contiennent essentiellement du cobalt (20 %) et un peu de lithium, la SNAM et Eurodieuze produisent des résidus de cobalt (sels de cobalt, hydroxyde de cobalt) via des procédés pyrométallurgiques pour le premier, hydrométallurgiques pour le second. De son côté, Récupyl propose un procédé hydrométallurgique de séparation du cobalt et du lithium afin de récupérer les deux métaux à 99 % sous forme de poudres de cobalt et de lithium. En 2014 SNAM et le CEA ont conclu un partenariat pour améliorer les procédés de récupération des terres rares (La, Ce, Nd, Pr), de cobalt, de nickel, de cuivre, de l'aluminium, et du manganèse dans des batteries Nickel-Métal-Hydrure et Lithium-Ion.
Enfin, la société KBI compte au moins dix ans avant que le marché du recyclage des batteries Li-ion ne devienne viable, et étudie ainsi également la solution du réemploi des batteries Li-ion en lieu et place de leur recyclage, en partenariat avec Toyota.
Sylvain Guignot
Sources
1. Laboratoire d'analyse et d'architecture des systèmes https://www.laas.fr/public/fr
2. HybridCars.com (2013). https://www.hybridcars.com/americans-buy-their-3000000th-hybrid/
3. JAMA Japan Automobile Manufacturers Association Inc. (2014). The motor industry of Japan 2014. www.jama-english.jp/
4. The International Council of Clean Transportation (2013). European Vehicle Market Statistics. Pocketbook 2013. https://theicct.org/
5. Journal Officiel des Communautés européennes (2000). Directive 2000/53/CE du Parlement européen et du Conseil du 18 septembre 2000 relative aux véhicules hors d'usage, L 269.
6. Recyclage Récupération, Octobre-Novembre 2014.
7. http://www.japaneselawtranslation.go.jp/law/detail/?id=127&vm=04&re=02&new=1
8. Kumar V., Sutherland J.W. (2009). Development and assessment of strategies to ensure economic sustainability of the U.S. automotive recovery infrastructure. Resour. Conserv. Recycl., 53, 470 – 477.
9. http://www.europarl.europa.eu/
10. National Highway Traffic Safety Administration (2012). https://www.nhtsa.gov/laws-regulations/corporate-average-fuel-economy
11. JAMA Japan Automobile Manufacturers Association Inc. (2014). 2013 report on environmental protection efforts. Promoting sustainability in road transport in Japan. http://www.jama-english.jp/
12. Recycling International (2014). Innovation shifting into high gear. http://www.recyclinginternational.com/
13. Recyclage Récupération (2014). VHU Performances de recyclage à l’étude.
14. Recyclingportal 320° (2014). Verwertung von Elektrofahrzeugen – experten untersuchen Recylingpotenziale. https://320grad.de/
15. https://ec.europa.eu/environment/waste/batteries/
16. U.S. Department of Energy (2011). Critical Materials Strategy. https://www.energy.gov/
17. Gaines L., Nelson P. (2009). Lithium-Ion Batteries: Possible Material Demand Issues. Argonne National Laboratory. http://www.transportation.anl.gov/pdfs/B/584.PDF.
18. Mineta National Transit Research Consortium (2014). Remanufacturing, repurposing, and recycling of post-vehicle application lithium-ion batteries. MNTRC Report 12-20. https://transweb.sjsu.edu/mntrc/
19. Gaines L. (2011). Recycling of Lithium-ion batteries.
http://www.istc.illinois.edu/about/SustainabilitySeminar20111115.cfm
20 Electronic Engineering Times (2013). Honda recycles rare earth metals from hybrid car batteries. https://www.eetimes.com
21. Gaines L. (2014). A look through the crystal ball at the future of automobile battery recycling. Argonne National Laboratory. http://www.transportation.anl.gov/
22. Automotive News (2012).Replacing Prius batteries can be good for the environment…and sales. http://green.autoblog.com
23. Gaines L., Dunn J.B., James C. (2013). Can automotive battery recycling help meet critical material demand? IEA HEV Task 19 Workshop. Davos, Switzerland.
24. ADEME (2011). Etude de la seconde vie des batteries des véhicules électriques et hybrides rechargeables. www.ademe.fr
25. ConsumerReport.org (2013). What happens to electric car batteries when the car is retired? - Recycling would help offset production impacts of batteries. https://www.consumerreports.org
26. Sacramento Business Journal (2012).Car makers prepare to recycle, reuse hybrid batteries.
27. https://reneweconomy.com.au/solar-storage-system-using-repurposed-ev-batteries-set-go-japan-46230/