Sommaire
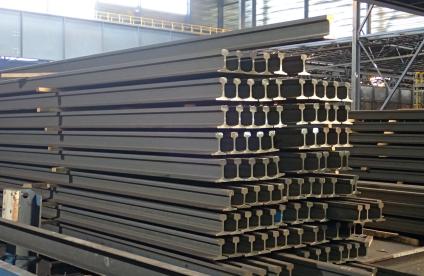
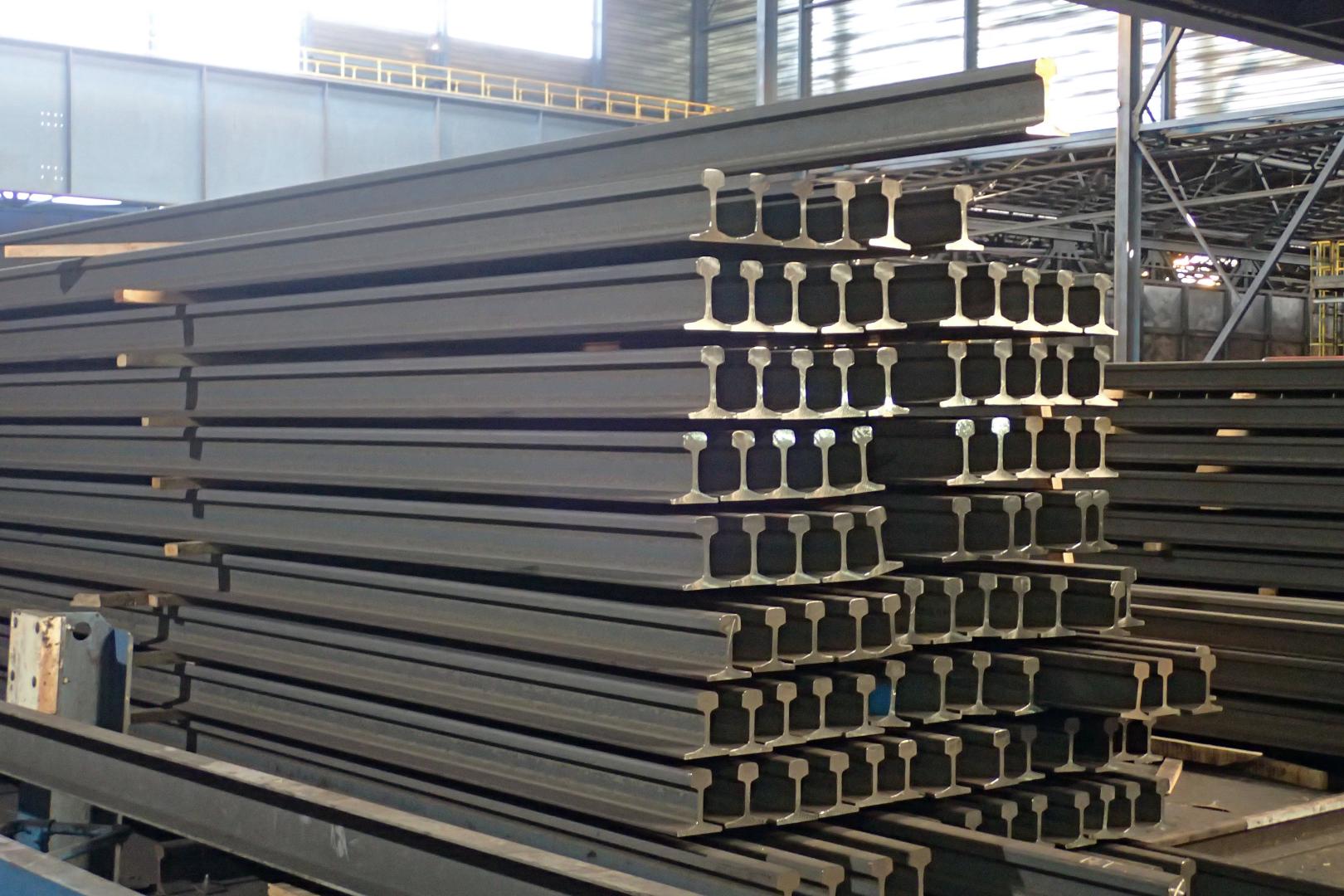
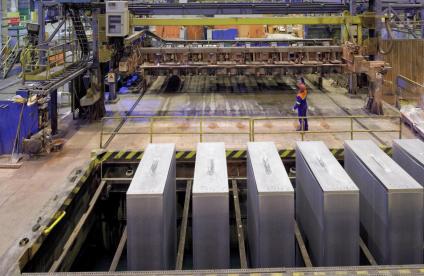
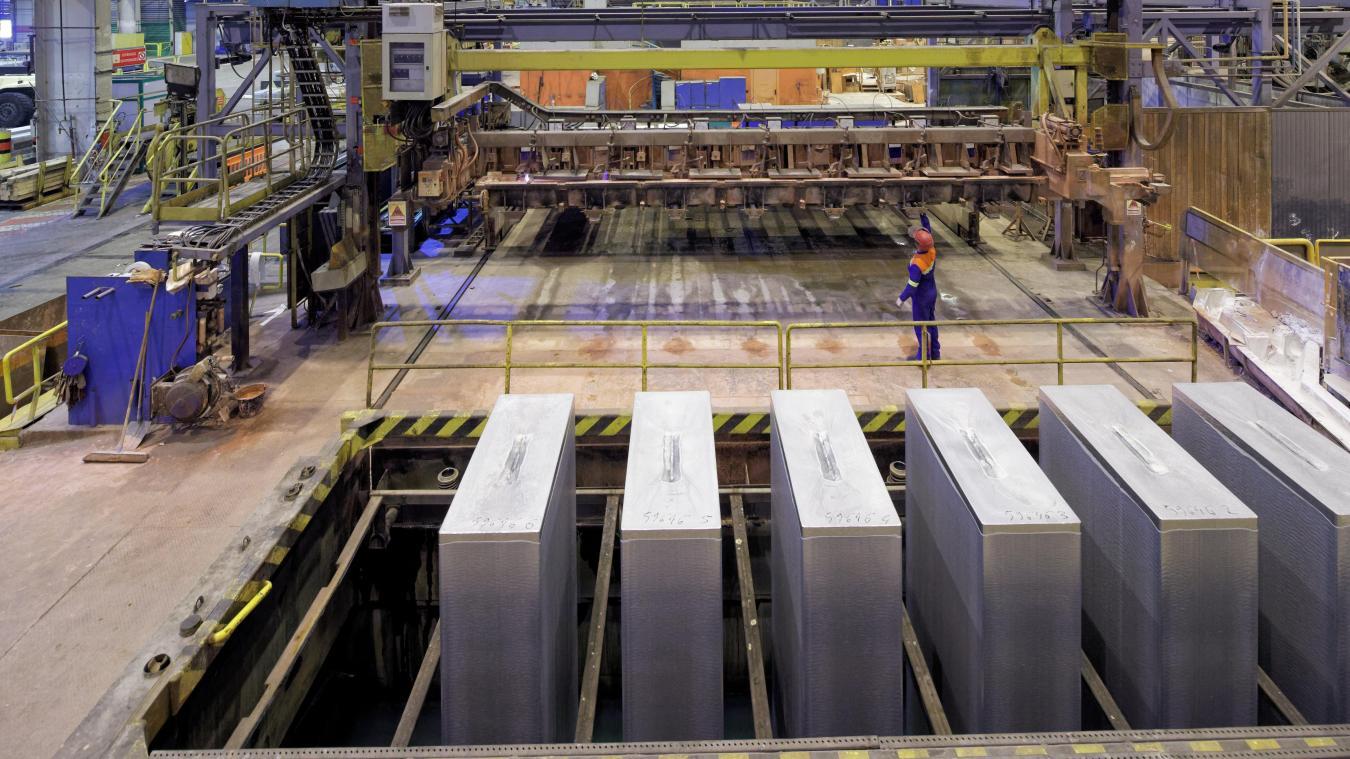
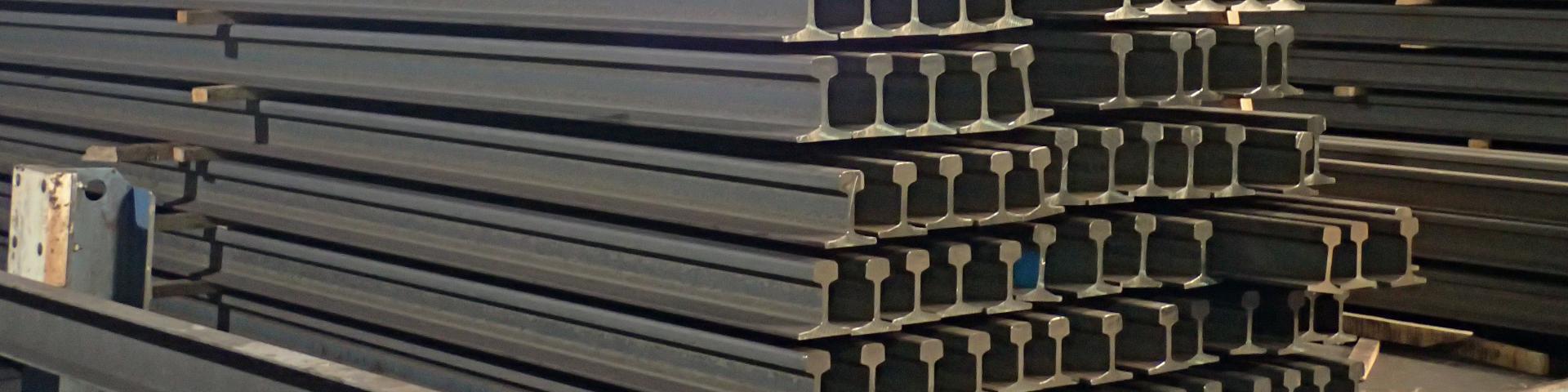
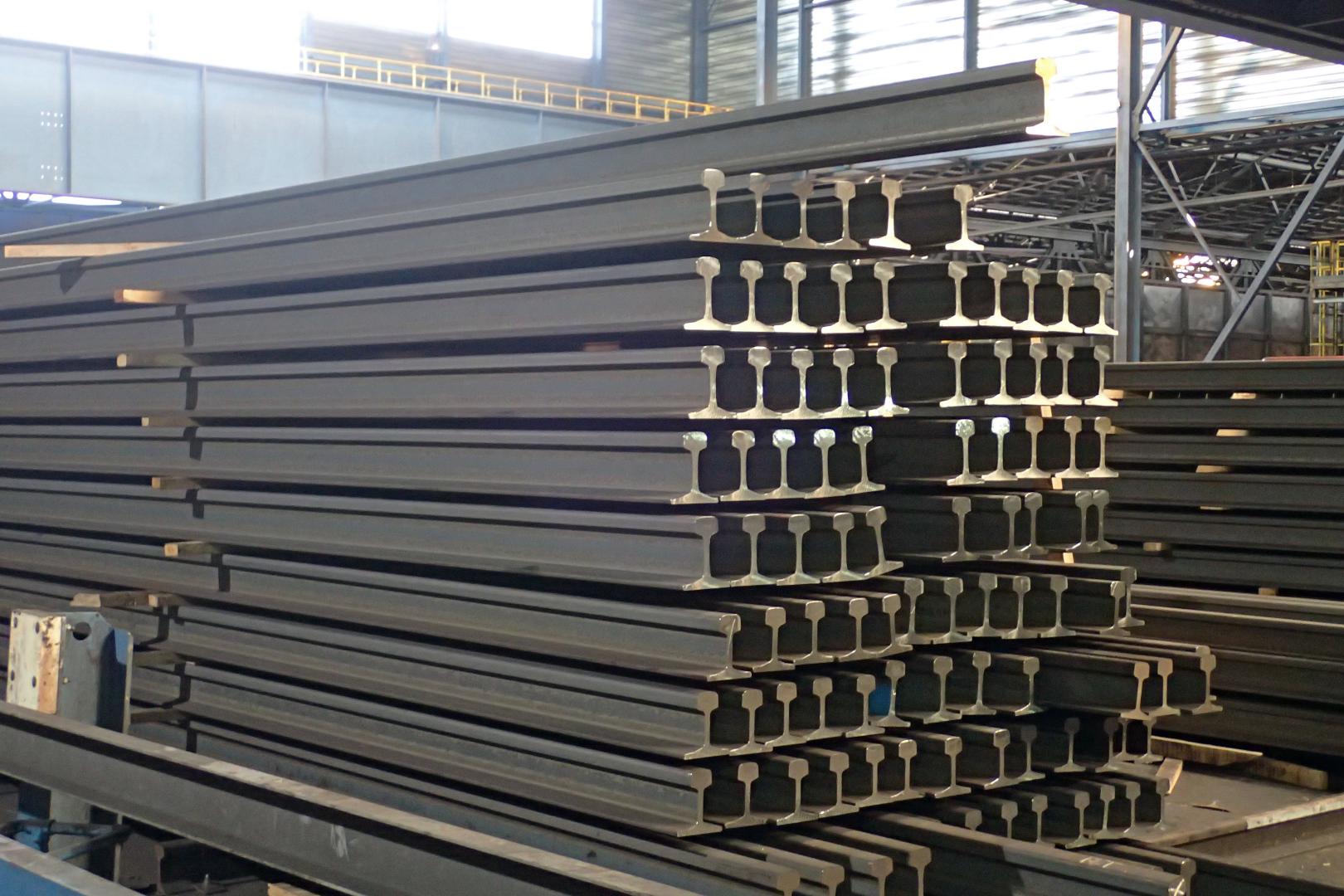
La première transformation en France
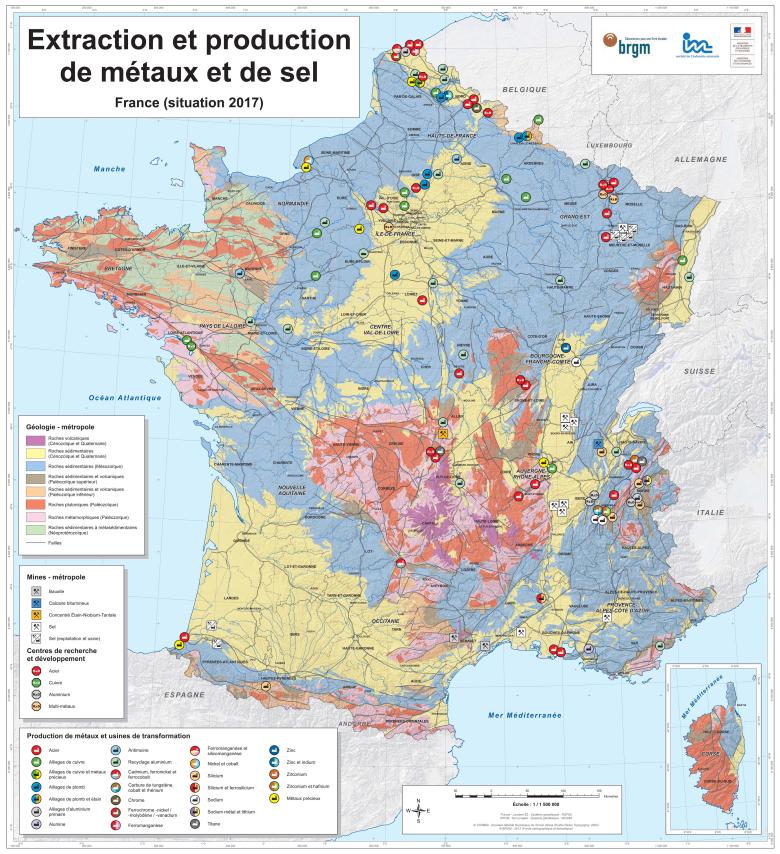
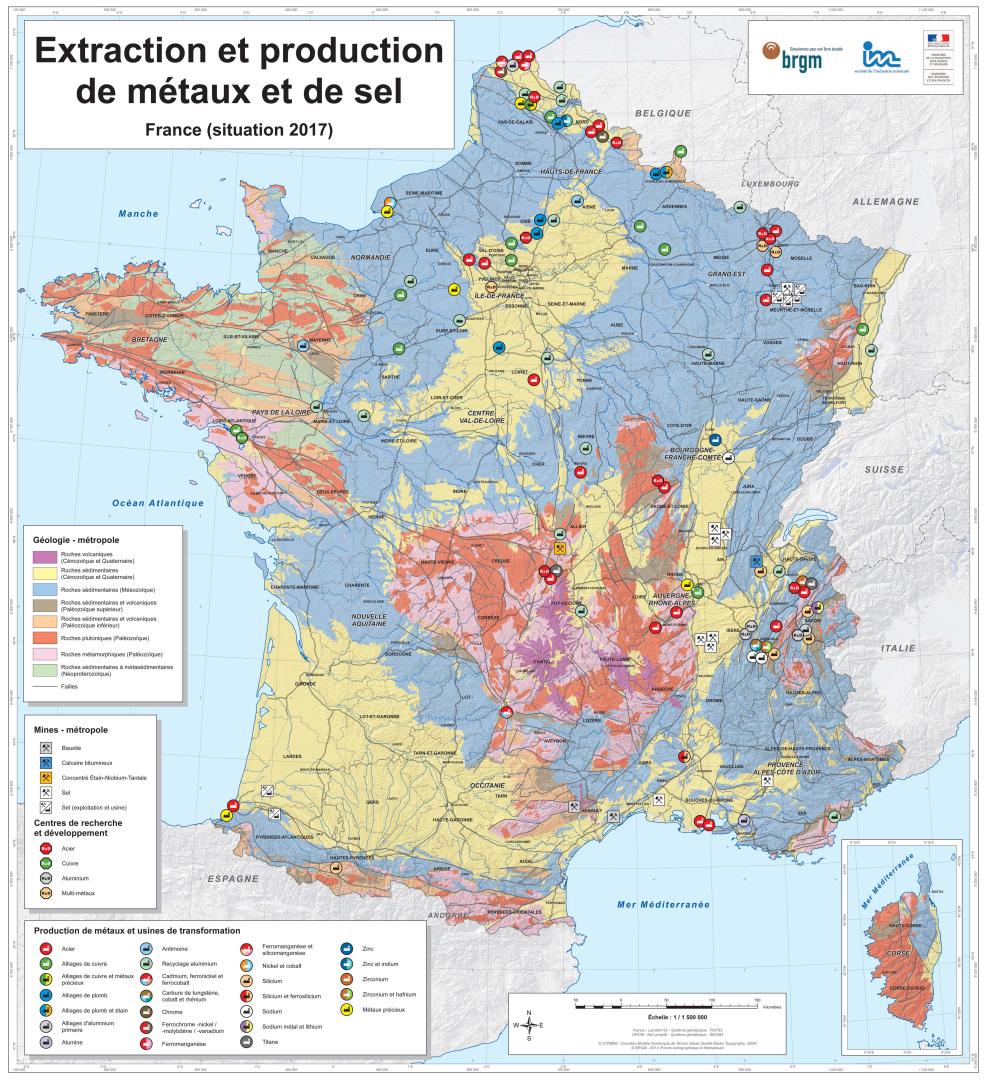
Carte des usines de première transformation de substances minières en métropole - 2017
BRGM-MTE-MEFR-SIM
Première transformation des substances minières en France
La sidérurgie : métallurgie du fer
L'industrie sidérurgique française s'appuie sur un large tissu industriel, dont la plupart des groupes sont internationaux (comme ArcelorMittal, Celsa, Dillinger, NLMK, Riva, Saint-Gobain, Schmolz et Bickenbach). Tous les types d'outils employés pour la fabrication de l'acier et des produits en acier sont utilisés en France : hauts-fourneaux, convertisseurs, fours électriques, installations de laminage à chaud, installations de laminage à froid et installations de revêtements métalliques et/ou organiques.
La filière française permet ainsi la production de la quasi-totalité des types de produits en acier. Ses différentes composantes présentes sur l'ensemble des segments du marché de l'acier peuvent être, selon le type de produit, classées en trois catégories :
- Produits longs : 4,1 millions de tonnes en 2017 (aciers d'armature pour le béton, profilés et poutrelles pour bâtiment, tubes, rails).
- Produits plats en aciers hors inoxydables : 11,5 millions de tonnes en 2017 (construction, laminés à froid et revêtus, profilés pour bâtiment, tôles quarto et électriques).
- Aciers spéciaux : 1 million de tonnes en 2017 (outillage, aéronautique, haute technologie, automobile et mécanique) dont aciers inoxydables (matériaux de hautes performances, superalliages, coutellerie, réfractaires).
Les métaux non ferreux
En France, la première transformation des métaux peut se faire à partir de minerais directement exploités en métropole et en Outre-mer (Guyane, Nouvelle-Calédonie) ou à partir de minerais importés puis transformés en France.
- Ainsi, un concentré d’étain-tantale-niobium est produit sur le site d’Échassières (Allier) après un traitement minéralurgique. Le concentré servira après traitement métallurgique à la confection de produits utiles à l’électronique, ou encore à la confection de superalliages.
- Le cobalt et le nickel extraits en Nouvelle-Calédonie serviront une fois transformés, à la fabrication de superalliages ou encore au secteur automobile et à la chimie, mais aussi à la production d'acier inoxydable, véritable "matériau du quotidien", contribuant à l'hygiène en cuisine.
- L’or, notamment extrait en Guyane, est utile à la joaillerie et à l’électronique. D’autres substances minières sont exploitées et transformées en produits non métalliques en France, comme la bauxite pour l’industrie cimentière, et les calcaires bitumineux pour l’industrie cosmétique et pharmaceutique.
La France transforme aussi des minerais métalliques importés d’autres pays : antimoine, argent, bauxite, chrome, cuivre, indium, manganèse, plomb, titane, tungstène, ou zinc.
Le sel
Présent dans le sous-sol français, le sel est exploité depuis plusieurs siècles par travaux miniers souterrains et par dissolution. Près de 7 millions de tonnes sont extraites chaque année pour alimenter de nombreuses filières industrielles et contribuer à la production de :
- Carbonate et bicarbonate de sodium indispensables à la fabrication de verre, de détergents, de comprimés effervescents et dans le traitement des fumées des incinérateurs ;
- Soude caustique, issue d’une transformation chimique du sel, indispensable aux industries des savons, lessives et détergents, du papier, de la métallurgie, des encres et colorants ;
- Chlore, une des matières premières de l’industrie du plastique PVC, employée aussi dans la fabrication des produits désinfectants ou blanchissants ainsi que dans divers solvants.
Le sel intervient aussi dans des applications pharmaceutiques et de santé spécifiques, et plus directement pour l’adoucissement de l’eau, le déneigement des routes ou encore en agriculture (conservation des fourrages, alimentation animale).
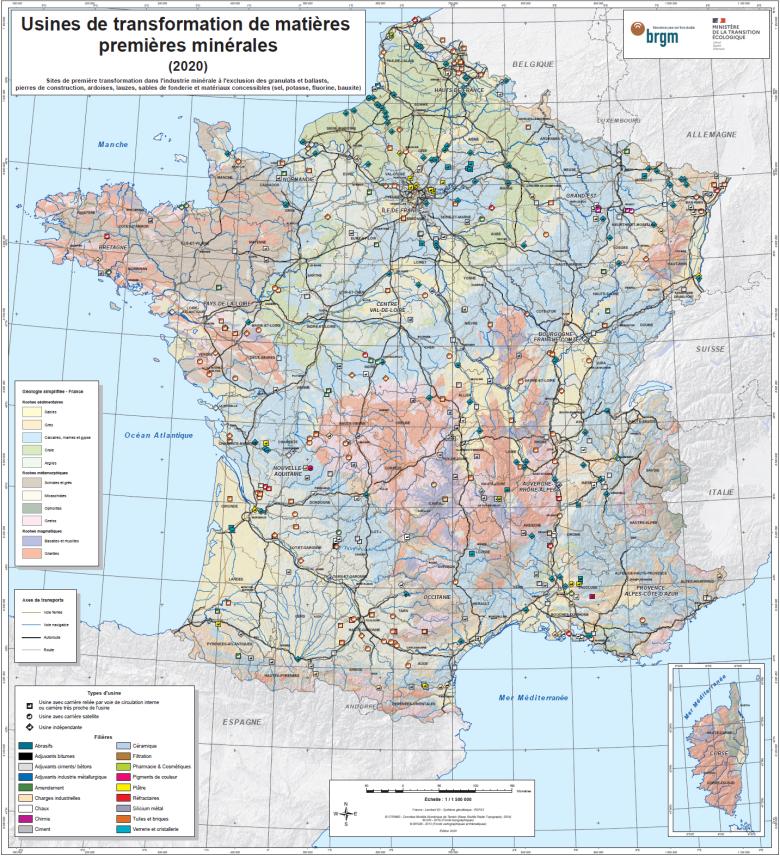
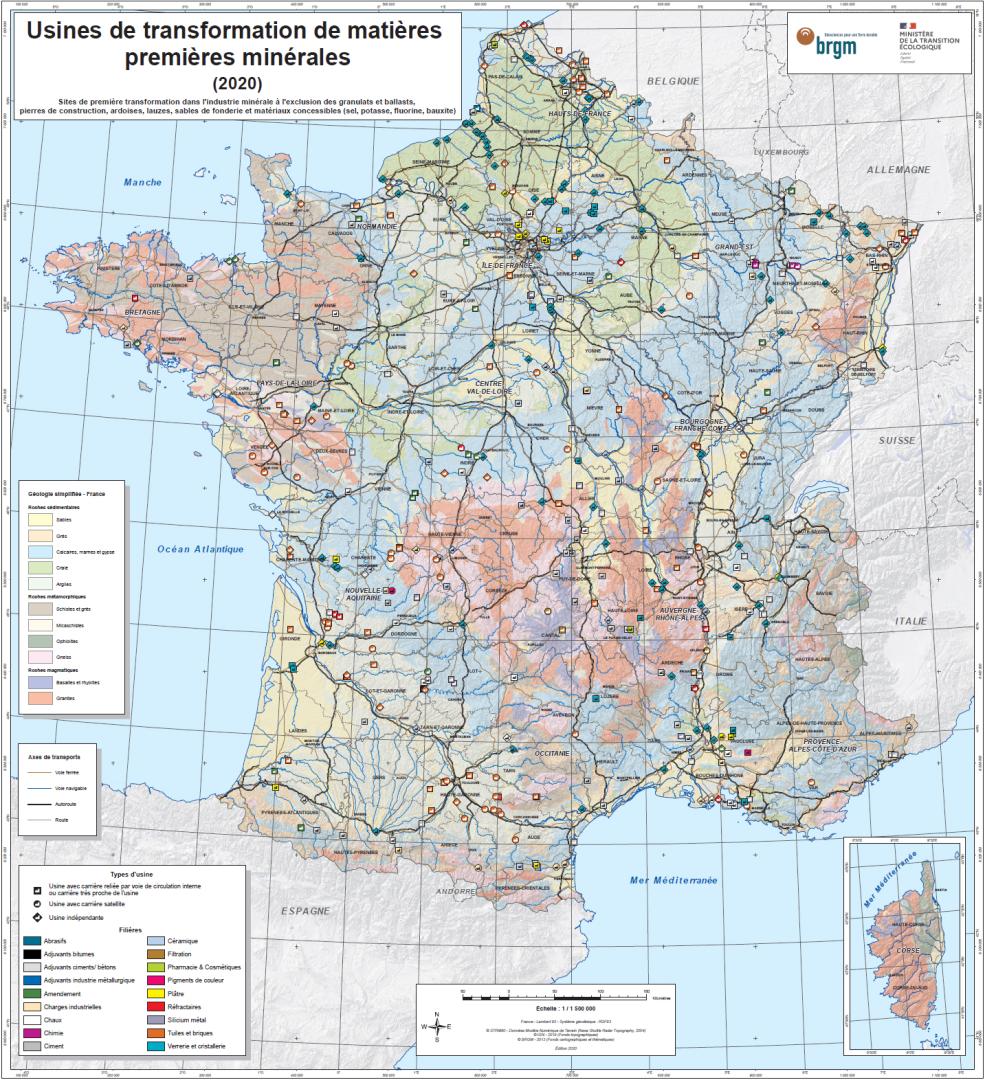
Carte des usines de première transformation des substances de carrières (à l'exclusion des granulats et ballasts, pierres de construction, ardoises, lauzes, sables de fonderie et substances minières) - 2019
BRGM-MTE
Première transformation des substances de carrières
En France, près de 400 usines de transformation participent à la filière des roches et minéraux industriels extraits en carrières. Ces usines sont des Installations Classées pour la Protection de l’Environnement (ICPE) et se répartissent selon 18 filières industrielles : ciment (42 usines), adjuvant pour ciment/béton (35), adjuvant pour bitume (1), chaux (30), plâtre (14), tuile et brique (92), céramique (15), réfractaire (9), pigment de couleur (2), adjuvant pour l’industrie métallurgique (1), silicium métal (9), verrerie (96), charge industrielle (15), pharmacie et cosmétique (3), amendement (22), filtration (7), chimie (4), abrasif (2).
Les usines peuvent se situer sur le site d’extraction et être parfois reliée par une voie de circulation interne (moins de 5 km). D’autres usines peuvent être alimentées par une ou plusieurs carrières satellites (plus de 5 km entre l’usine et la(es) carrière(s)). Des usines peuvent être aussi totalement indépendantes du site d’extraction. Pour les deux premières catégories, la carrière et l’usine appartiennent au même groupe ou à la même entreprise. En revanche la logique est différente pour les usines indépendantes, qui achètent leurs matières premières auprès d’entreprises tiers (majoritairement auprès de carriers, mais également auprès de négociants ou d’autres industriels, d’autant plus dans les filières à plus forte valeur ajoutée, telle que la papeterie ou la verrerie).
En ce qui concerne les usines avec carrière(s) exploitée(s) par le même groupe, l’alimentation en matières premières, la qualité et le prix en entrée d’usine sont maîtrisés. Cela permet d’assurer des investissements souvent conséquents dans l’industrie en s’appuyant sur une ressource prouvée et contrôlée. Ce n’est pas le cas pour les usines indépendantes qui dépendent de contrats de fournisseurs et sont exposées à une variation des prix ou à une baisse de quantité et/ou de qualité.
Il faut également noter que certains produits à haute valeur ajoutée peuvent être transportés sur des distances importantes entre la carrière et l’usine, parfois de plusieurs centaines de kilomètres.
Concentré d'andalousite vendu sous l'appellation "kerphalite" à Glomel (Côtes d'Armor)
© BRGM - N. Charles
Qu'est-ce que la « première transformation » ?
Sans définition officielle, le périmètre de la première transformation peut néanmoins être déduit de la Nomenclature d’Activité Française (NAF).
À l’amont de la première transformation, la nomenclature distingue « l’extraction et les industries extractives » (section B) qui incluent les opérations de préparation des matières brutes pour leur commercialisation, telles que concassage, broyage, nettoyage, séchage, tri et concentration des minerais.
La première transformation fait partie quant à elle de « l’industrie manufacturière » (section C) mais la limite entre première et seconde transformation relève plus de conventions à l’intérieur de chaque secteur que d’une définition univoque. Les sites industriels accueillent souvent différentes étapes de transformation, ce qui réduit fortement la précision de la distinction, et en limite l’utilité. En effet, des sites industriels comme les cimenteries peuvent regrouper des activités extractives (carrières) et de première transformation (fours) et des sites métallurgiques réalisent un ensemble d’opérations pouvant aller de l’élaboration et de l’affinage du métal jusqu’à la production de pièces semi-finies (fonderie, forge, usinage).
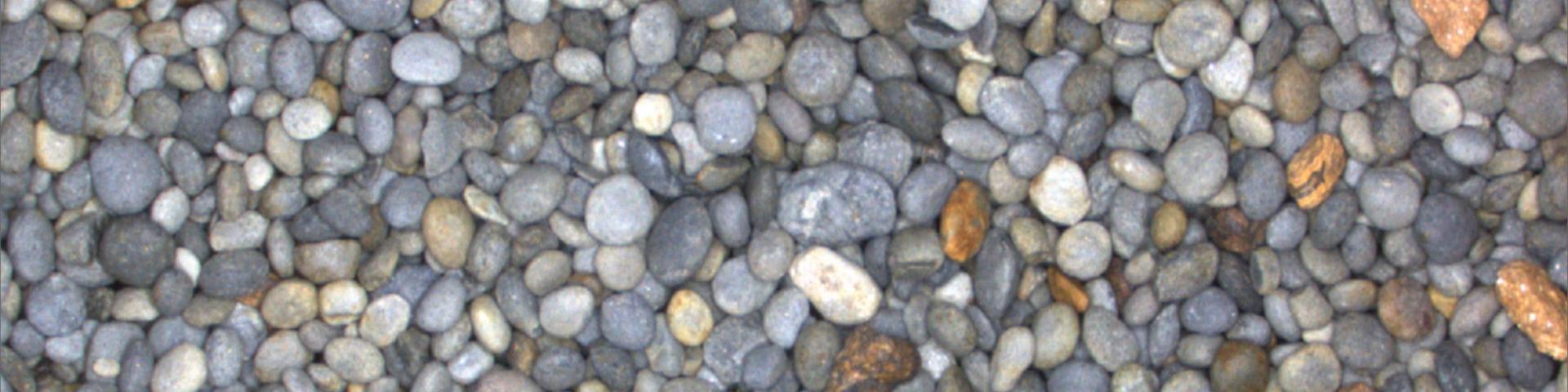
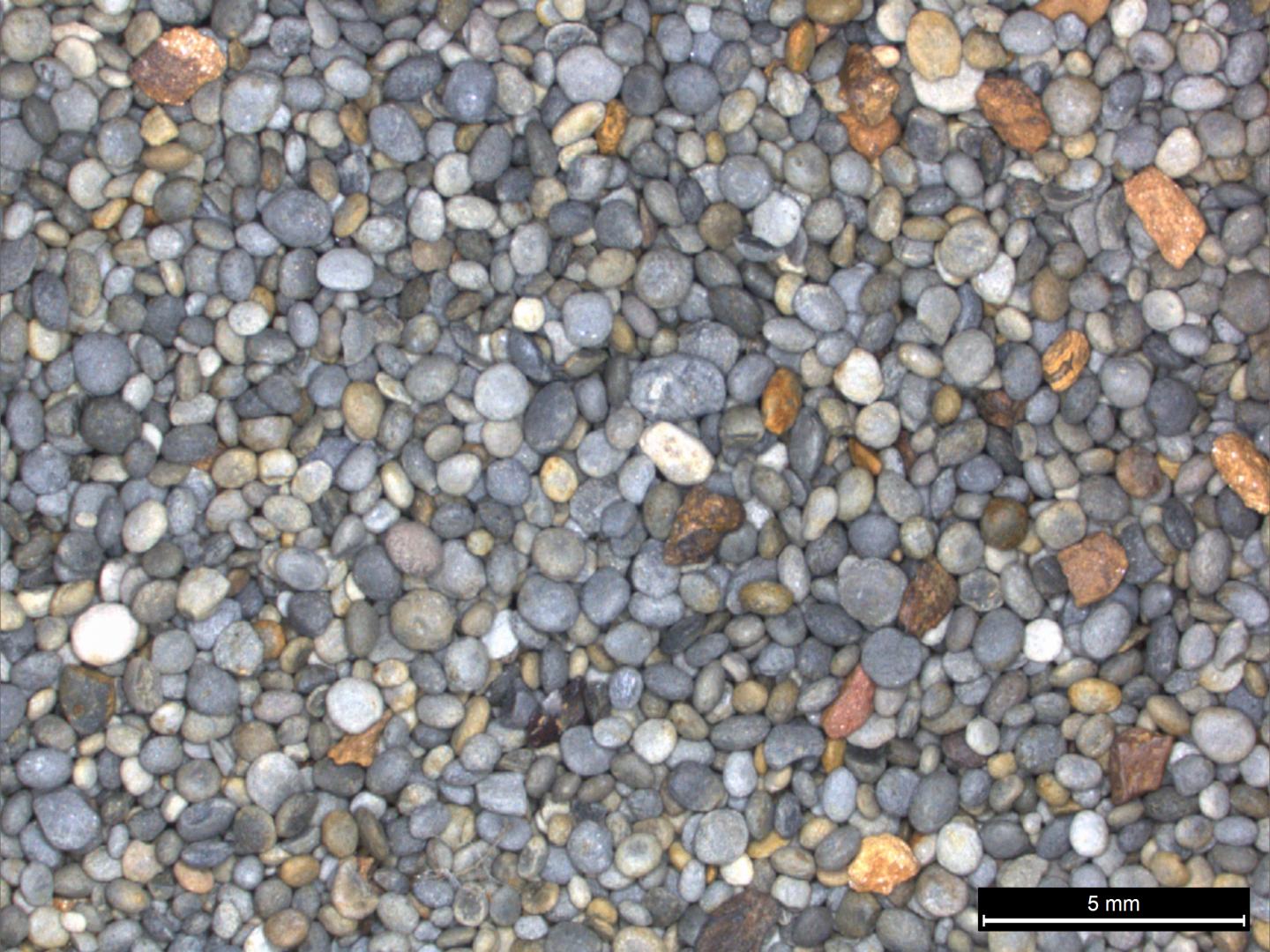
Minéralurgie
Réduction granulométrique du minerai : la comminution
Un gisement est un corps naturel issu de processus géologiques qui conduisent à la formation d’un ensemble plus ou moins complexe de roches et de minéraux. Une fois le minerai extrait, tous les minéraux qu’il contient ne sont pas tous valorisables et il apparaît alors nécessaire de les séparer pour n’en conserver que la partie utile.
La comminution est la première étape du traitement minéralurgique qui conduit à une réduction granulométrique. Le minerai tout-venant extrait de la mine ou de la carrière passe par de multiples opérations de concassage puis de broyage avec l’utilisation de plusieurs types de machine par voie sèche et/ou par voie humide :
- Concassage primaire avec notamment des concasseurs à mâchoires ou giratoires ;
- Concassage secondaire avec des concasseurs à cônes pour obtenir des grains centimétriques ;
- Concassage tertiaire (notamment pour les minerais métalliques), généralement effectué à l’aide de broyeurs à boulets ou à billes pour obtenir une granulométrie de l’ordre de quelques micromètres.
La taille finale des particules est déterminée à partir d’observations minéralogiques et de tests en laboratoire permettant de déterminer la « maille de libération ».
Cette maille de libération, obtenue par concassage puis broyage, vise à obtenir une taille de grain idéale pour :
- Libérer les minéraux valorisables des minéraux de la gangue (stérile) ;
- Générer des surfaces de grain fraîches ;
- Réduire la taille des grains afin d’augmenter leur surface spécifique qui améliorera le cas échéant les vitesses de transformation par voie hydrométallurgique ou pyrométallurgique.
Séparation et concentration des minéraux
Après la comminution, la phase de concentration permet de séparer les particules libérées en utilisant leurs propriétés physico-chimiques et ainsi produire un concentré de minerai qui peut à ce stade être directement commercialisable.
La séparation des minéraux à valoriser et le stérile est rendue possible par plusieurs méthodes :
- Séparation granulométrique. Elle permet de séparer les minéraux selon la taille des particules qui passent à travers une maille. Cela permet d’éliminer les résidus ou bien de rediriger les plus grosses particules vers l’étape précédente ;
- Séparation par milieu dense. Cette méthode consiste à séparer les minéraux par gravité à l’aide d’une liqueur dense (typiquement des densités de l’ordre de 3) ou d’une suspension de solide à une densité donnée (ex. magnétite, ferrosilicium). Elle est particulièrement utilisée pour les métaux lourds (or, tungstène, titane, niobium et tantale, etc.) ;
- Séparation par gravité. cette méthode consiste à séparer les minéraux par gravité de façon mécanique grâce à des appareils spécifiques (tables à secousse, spirales, sluices ou rampes de lavage, jigs, etc.) ;
- Séparation magnétique. Cette méthode utilise les propriétés magnétiques des minéraux et permet par exemple de séparer le quartz (non magnétique) des oxydes de fer et de titane (magnétite, hématite et ilménite), ou encore de trier des sables à rutile, ilménite et zircon. Cette méthode s’applique particulièrement aux minéraux ferreux.
- Flottation. Elle consiste à séparer les minéraux rendus hydrophiles ou hydrophobes par l’utilisation de réactifs. Une alimentation en air dans la solution liquide contenant le minerai permet de créer des bulles qui collectent les minéraux hydrophobes et les remontent à la surface, formant une mousse qui est aisément récoltée. Cette technique utilise soit des cellules mécaniques (cuves en acier) soit des cellules pneumatiques (généralement sous forme de colonnes de flottation).
- Tri optique. Il s’agit de sélectionner les minéraux à partir d’une ou plusieurs caméra(s) optique(s) selon des critères comme la couleur, la radioactivité ou la densité. Cette méthode s’est particulièrement développée ces dernières années grâce au progrès du calcul informatique.
Dans de nombreux cas, le minerai est traité en « pulpe », c’est-à-dire que de l’eau lui est ajoutée à la séparation. Pour récupérer uniquement le minerai concentré, cette eau est retirée par centrifugation, décantation, filtration ou séchage naturel. Il est alors prêt pour les traitements par voie métallurgique.
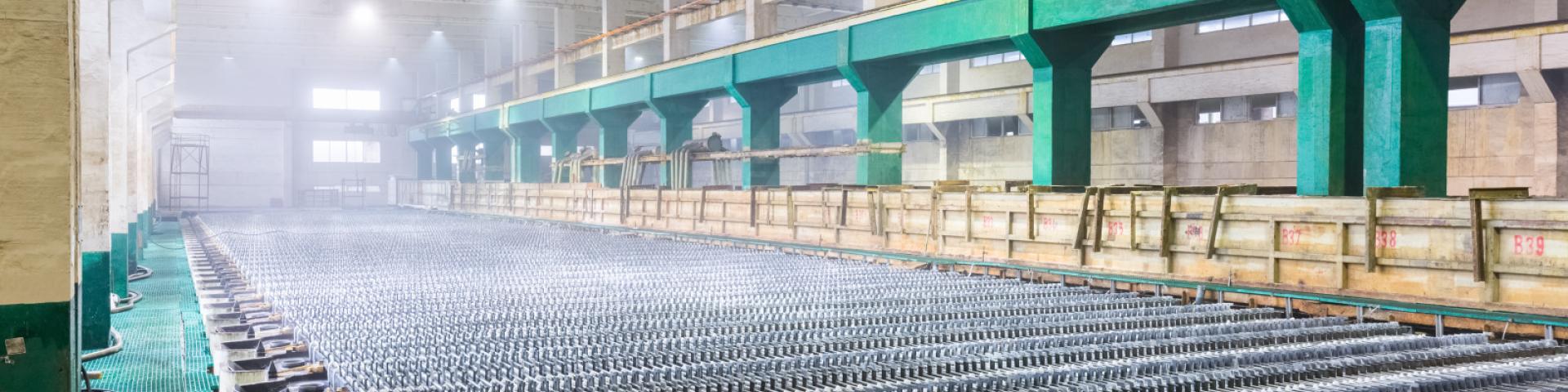
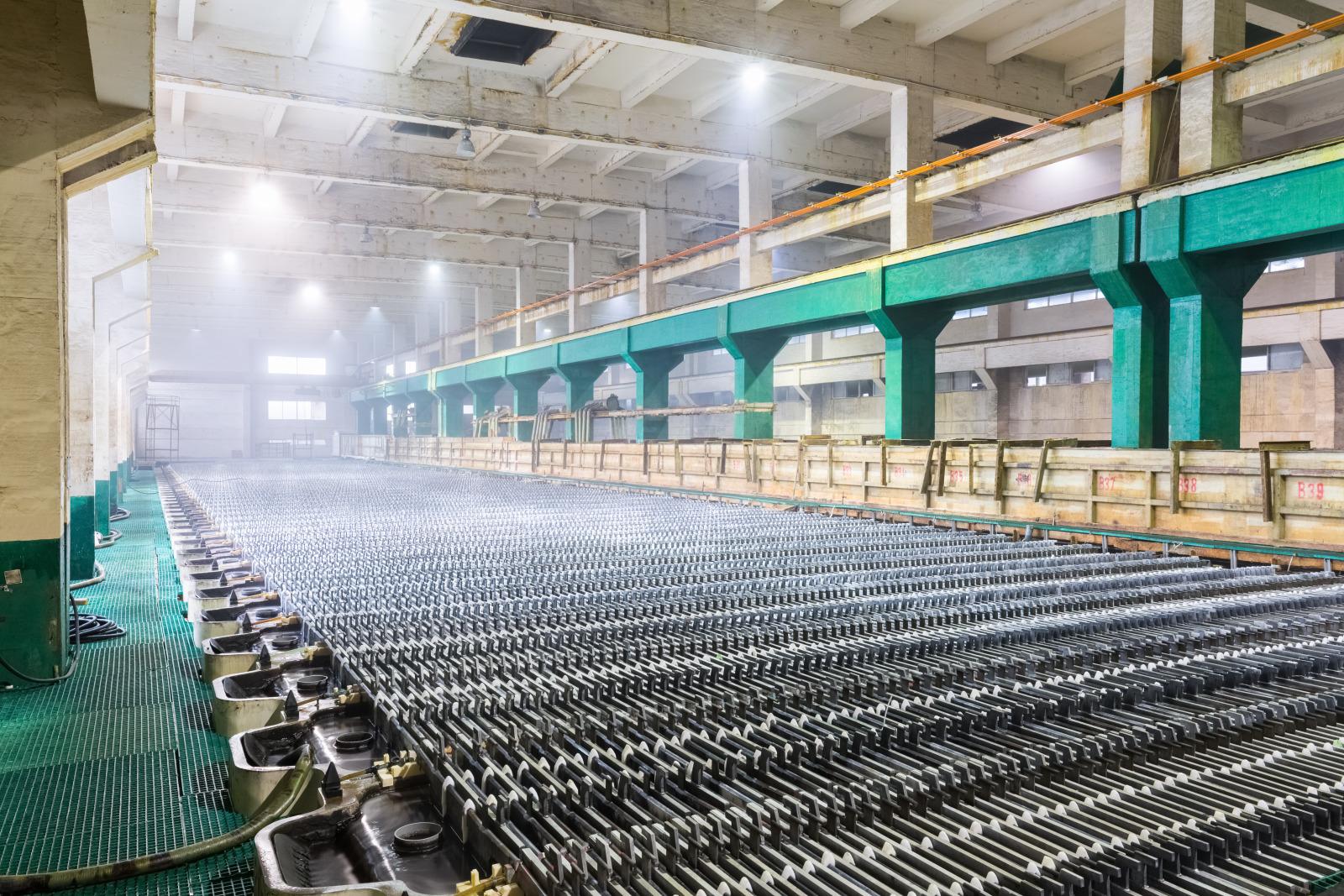
Métallurgie
Production de cathodes de cuivre par electrowinning, Skouriotissa, Chypre
© Guillaume Bertrand, BRGM
La métallurgie extractive
Pour extraire d’un minerai les éléments métalliques à valoriser, deux grands procédés sont utilisés :
- La pyrométallurgie. Ce procédé métallurgique (le plus ancien) consiste à transformer le minerai en le chauffant à très haute température (« grillage ») grâce à différentes sources d’énergie (gaz, électricité, charbon, etc.). L’objectif est d’éliminer l’oxygène présent dans les oxydes métalliques afin d’obtenir du métal : c’est le phénomène de réduction, par opposition à celui d’oxydation. Les éléments qui n’ont pas été réduits lors de la chauffe sont appelés communément scories ou laitier, et sont ensuite séparés du métal liquide par différence de densité. Le procédé pyrométallurgique se prête bien à des minerais « riches », c’est-à-dire à forte teneur en éléments valorisables.
- L’hydrométallurgie. Cette méthode par voie électrochimique (la plus récente, du début du XXe siècle), consiste à dissoudre un minerai solide (généralement réduit en poudre) pour le mettre en solution : c’est la lixiviation (d’où le préfixe « hydro »). Le métal ainsi solubilisé permet sa purification et peut faire appel, en dernière étape, à l’électrolyse au cours de laquelle, un courant électrique de forte puissance passe entre une anode et une cathode au sein de la solution contenant le métal dissous. Le métal valorisable est ensuite récupéré sur l’anode ou la cathode. D’autres étapes que l’électrolyse peuvent être ajoutées en fin du cycle d’hydrométallurgie, il s’agit d’étapes de purification avec des procédés d’échange ionique liquide ou solide (solvants ou résines). Le procédé hydrométallurgique est particulièrement efficace pour traiter des minerais contenant plusieurs éléments métalliques valorisables.
Un exemple de procédé hydrométallurgique : la biolixiviation
La métallurgie d’élaboration ou d’affinage
Cette étape permet d’affiner le métal en général sous sa forme liquide afin d’en faire un produit plus pur, dans la continuité de la métallurgie extractive. À la fin de ce cycle de traitement, la composition chimique du métal est stabilisée et celui-ci est coulé sous forme de lingots, de billettes ou de barres qui seront utilisés pour composer des alliages ou directement façonnés en pièces industrielles.
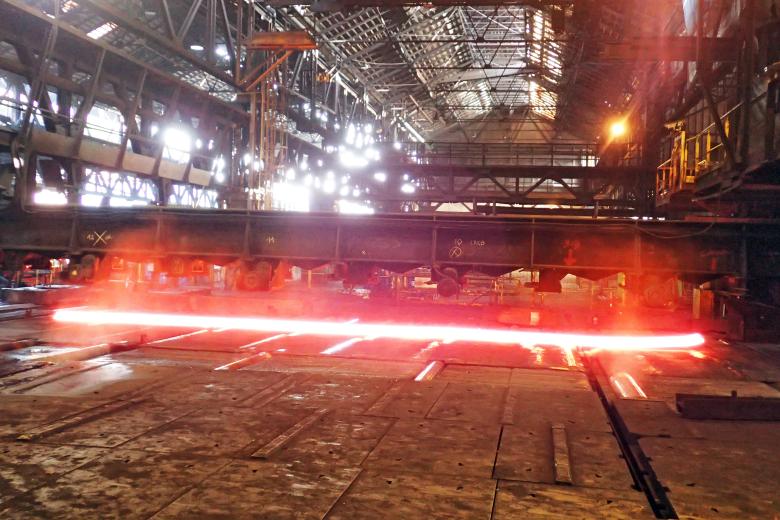
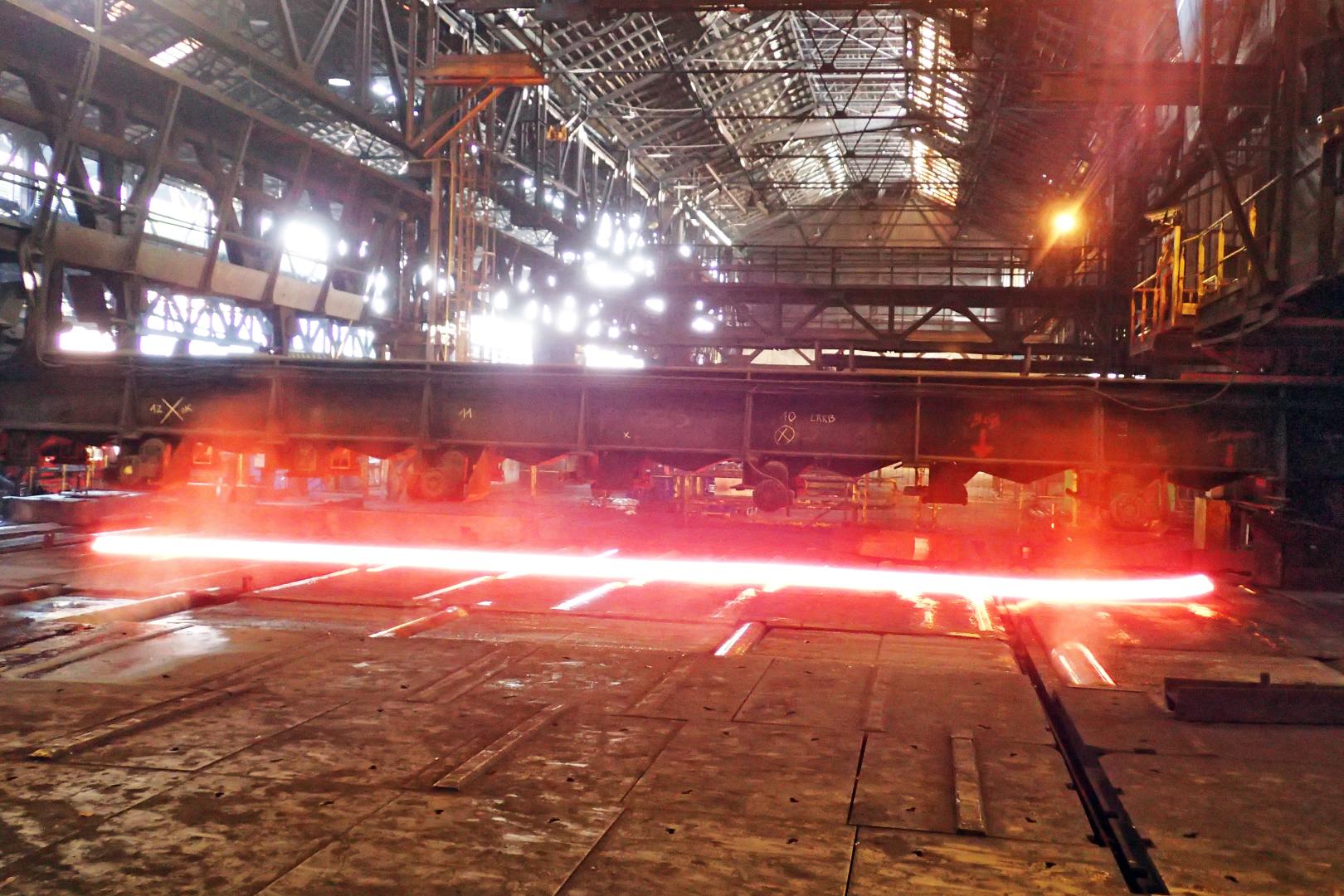
Rail incandescent après son passage au laminoir à l'usine d'Hayange (Liberty Steel)
BRGM - N. Charles
La métallurgie de transformation
Cette étape permet de conférer des propriétés mécaniques (élasticité, dureté, résistance, etc.) à un métal tout en lui donnant une forme (barres, fils, pièces matricées ou forgées). C’est une étape essentielle pour des marchés exigeants sur la qualité et les performances des métaux comme l’aéronautique, les transports et l’énergie.
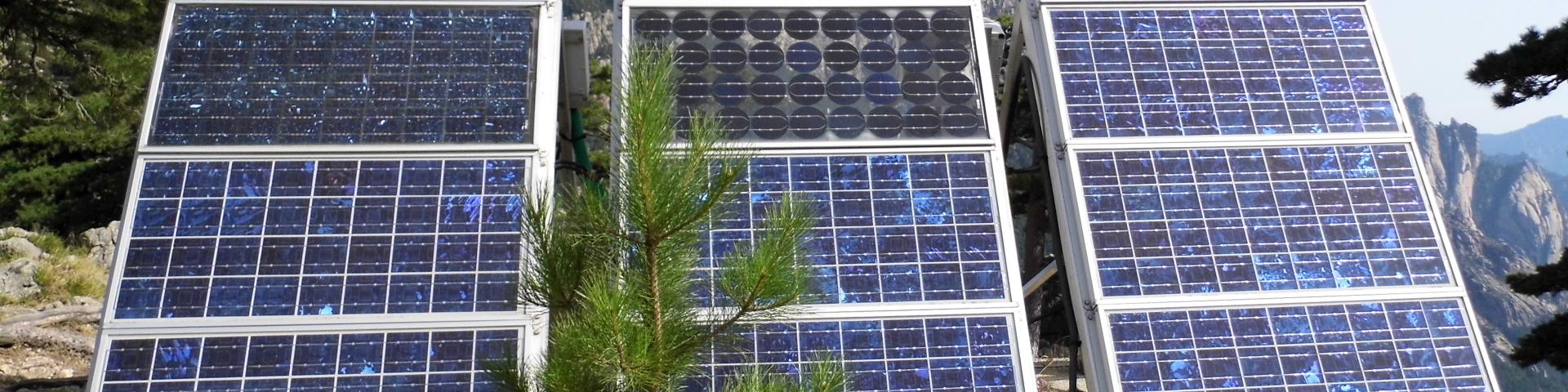
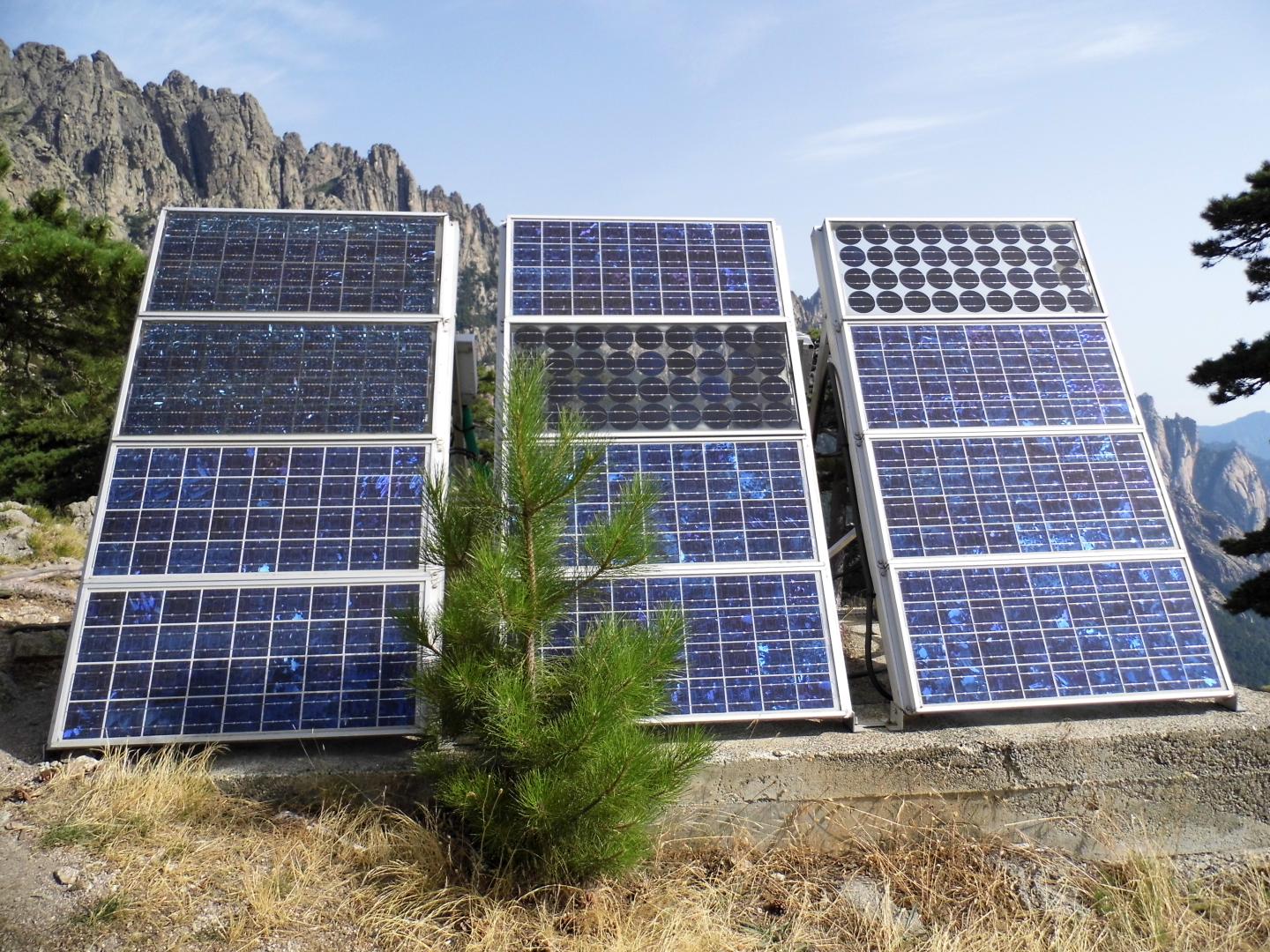
Usages des métaux et leur rôle essentiel dans la transition énergétique
L’industrie minière et métallurgique innove en continu afin de répondre aux enjeux de la transition énergétique et aux évolutions technologiques. Au sein des centres de recherche et développement et au travers de partenariats entre les secteurs public et privé, les procédés de fabrication et les performances des matériaux sont sans cesse améliorés garantissant l’approvisionnement en matières premières et transformées indispensables notamment à la transition énergétique (mobilité électrique, éolien, photovoltaïque, réduction de l’empreinte environnementale des constructions…). La consommation de métaux toujours plus diversifiés ne cessera de croître à l’avenir comme le soulignent de nombreuses études scientifiques et économiques. Le développement toujours plus important des nouvelles technologies dans les secteurs de la communication et de l’informatique, de la mobilité électrique ou des énergies dites renouvelables confirme cette tendance.